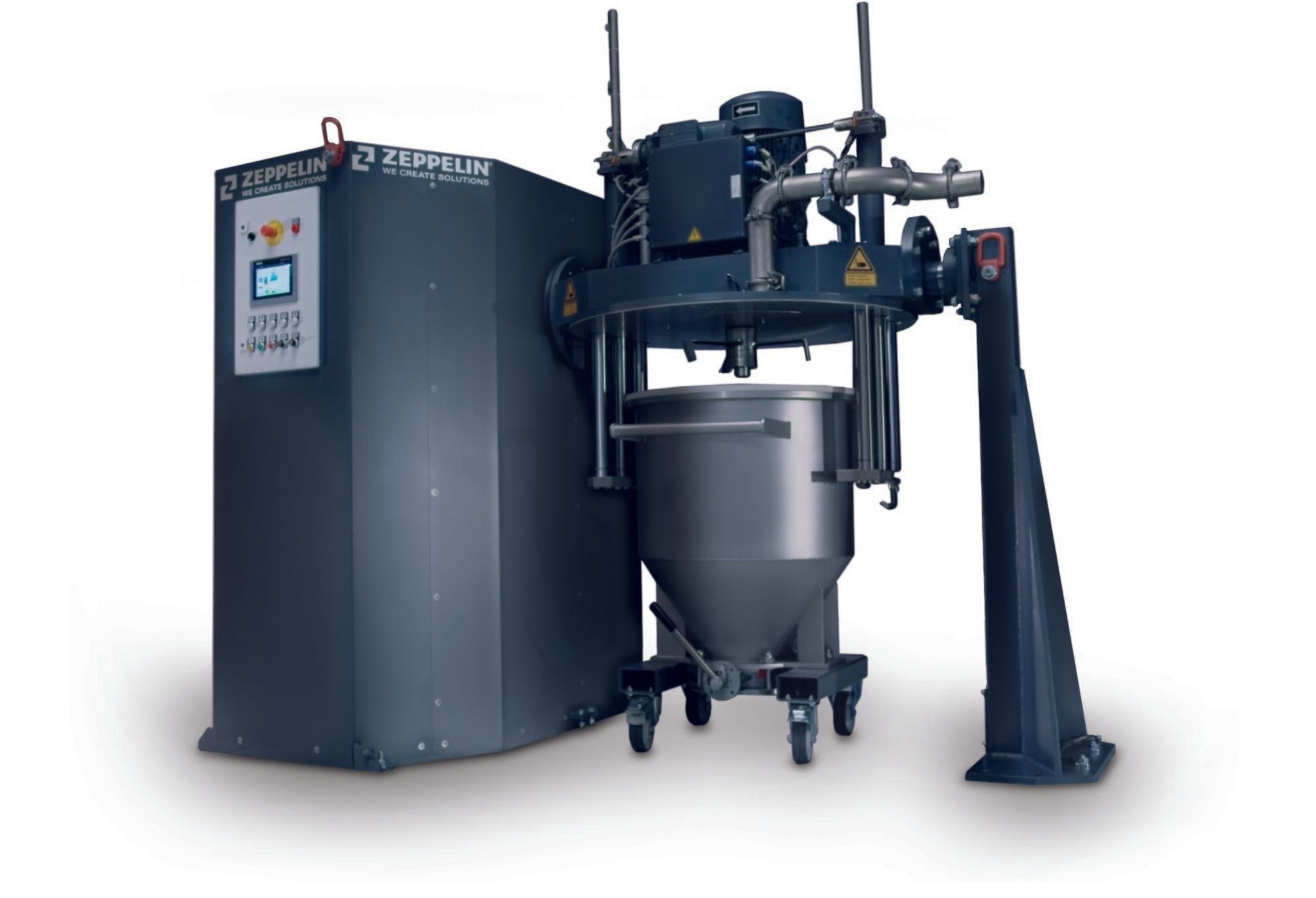
Container mixer CMQ
significantly increases your process productivity
Product changeover: fast and efficient
The innovative mixing concept of the container mixer CMQ significantly increases your process productivity. It not only enables more efficient operations, but also delivers exceptionally high-quality, deviation-free mixing results. Whether you are processing powder coatings, masterbatches, color concentrates, or compounds – the CMQ optimizes your mixing process. It is the first choice for frequent product changeovers, especially due to its cleaning-optimized design, which effectively prevents cross-contamination.
Key advantages at a glance:
- Innovative and patented* wing profile tool (*EP 3 342 480 B1)
- Maximum flexibility
- Designed for minimal cleaning effort
Options:
- Monitored automatic container grounding
- Vibration monitoring of bearings
- EU type-examination certificate for ATEX equipment category 1/3 D
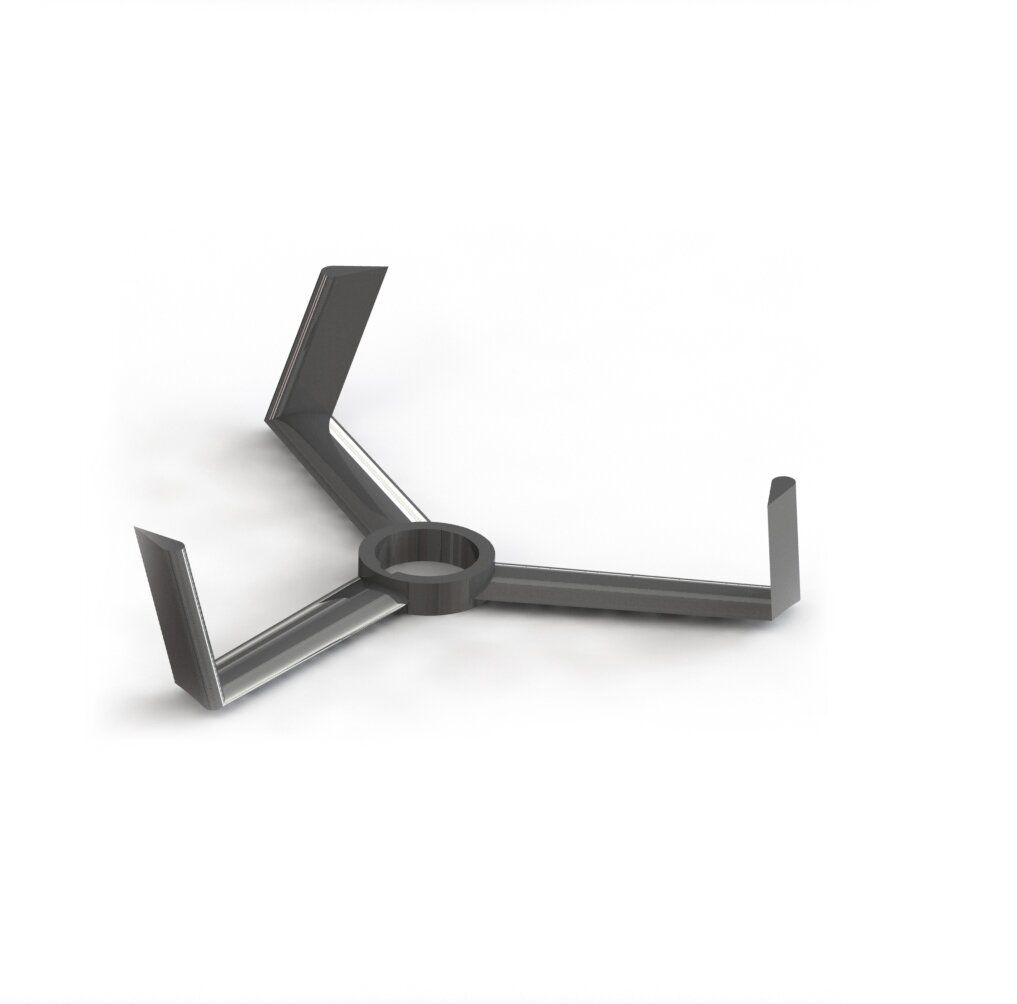
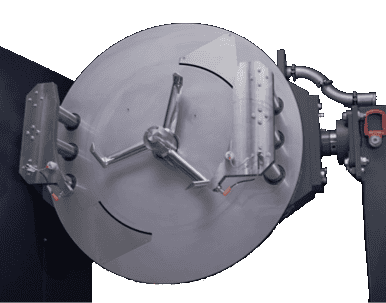
Application areas
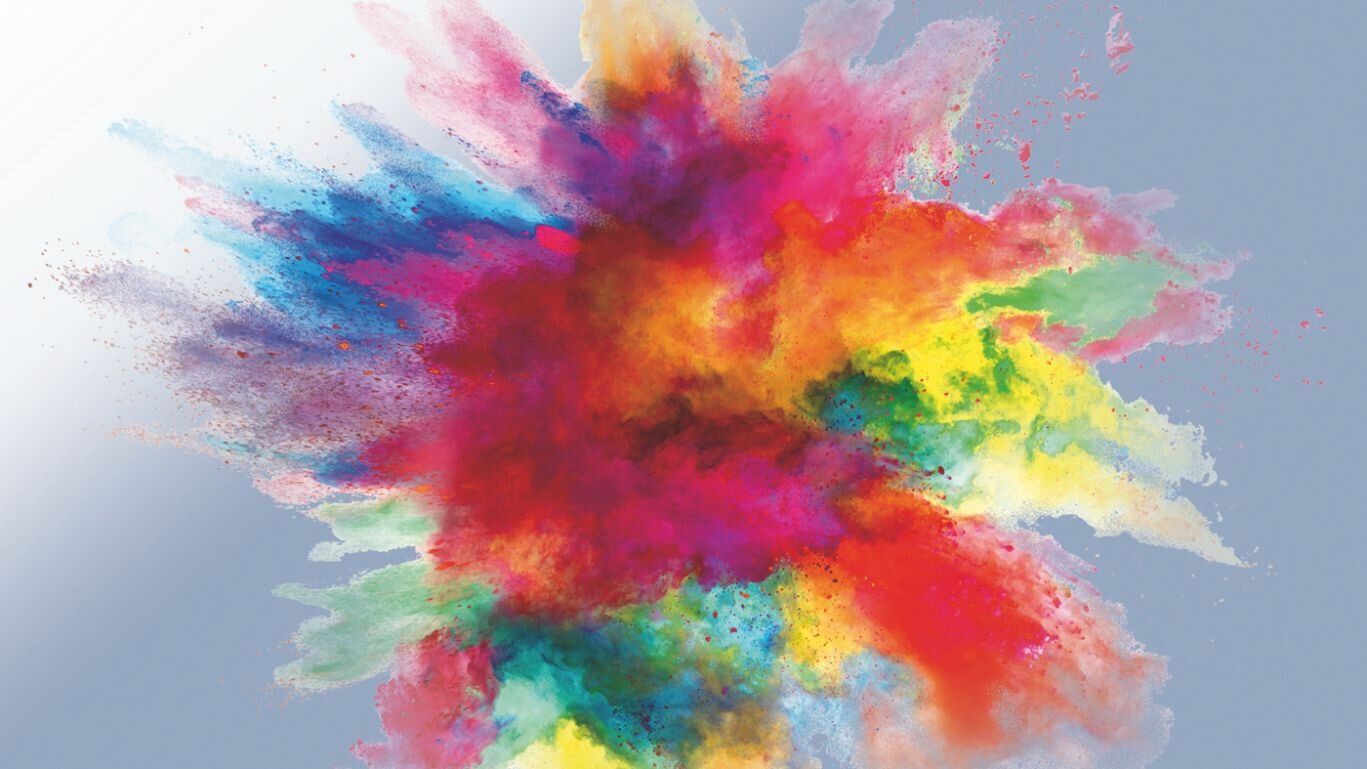
Powder coatings
In powder coating production, it is essential to create a high-quality premix before extrusion. The bulk materials are mixed with low energy input while ensuring effective dispersion of the pigments.
- Minimal temperature increase – ideal for temperature-sensitive base materials
- Excellent color ream and pigment dispersion
- Short cleaning times
- Safe operation in compliance with ATEX regulations
- Customizable batch sizes
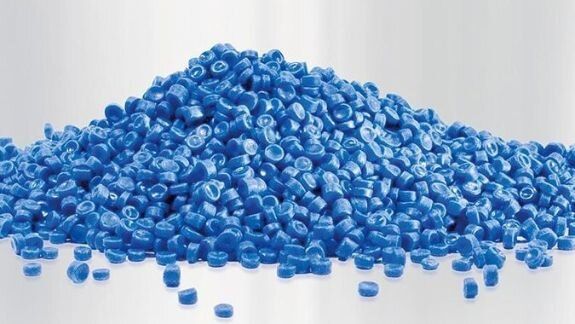
Additive masterbatches
Additive masterbatches are used in the plastics industry to improve the properties of plastics and to give them special functions such as UV protection, flame retardancy, antimicrobial properties, etc. By pre-mixing several additives into a homogeneous mixture, additives can be weighed and dosed more easily.
- Fast and effective homogenization
- Short cleaning times
- Safe operation in compliance with ATEX regulations
- Customizable batch sizes
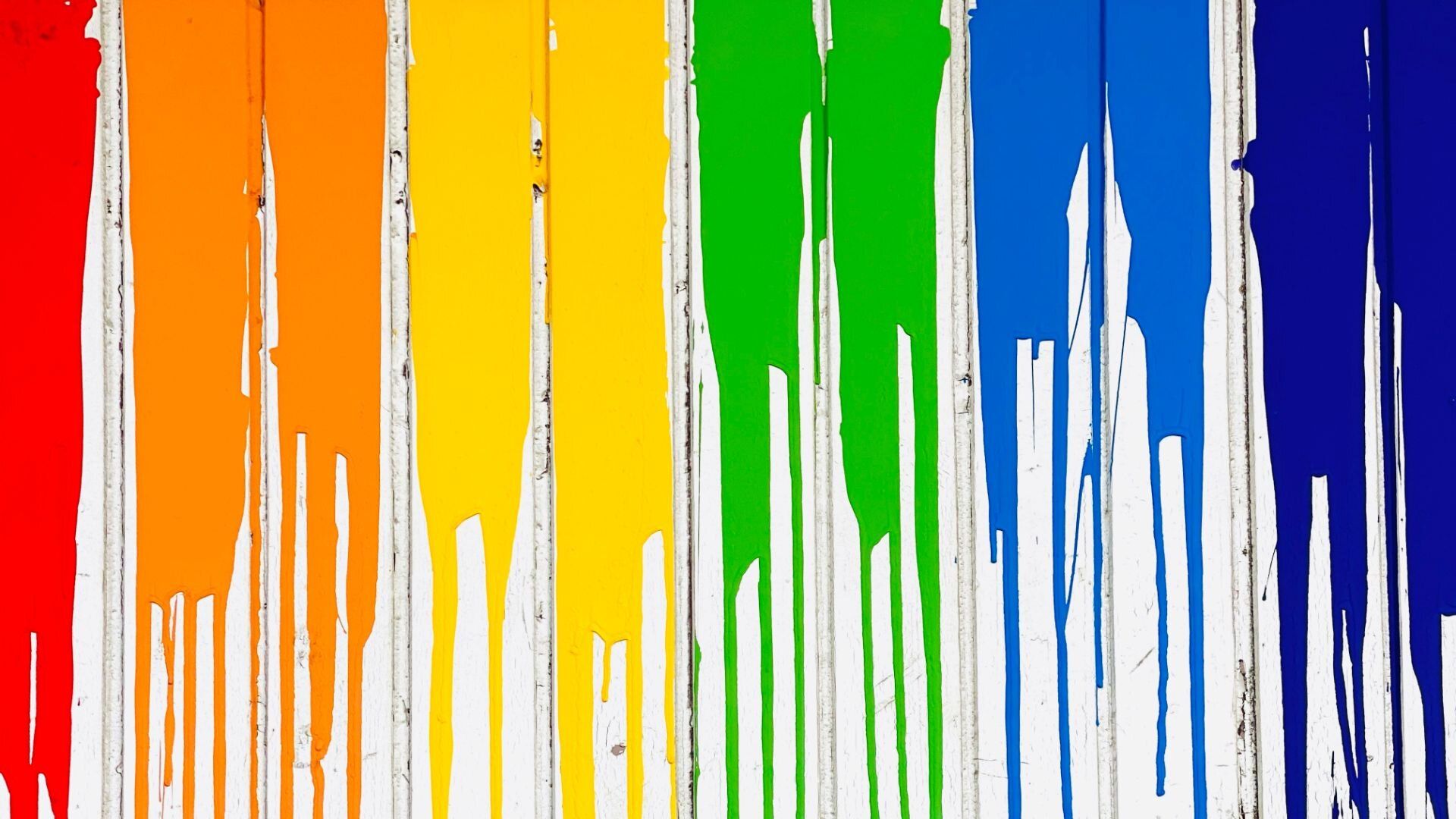
Color masterbatches
Color masterbatches are used in the plastics industry to color plastics efficiently and uniformly. The premix can therefore be weighed, dosed and then extruded more easily. The conventional process, which involves long kneading and heating times as well as complex machinery, is optimized so that all components are mixed, homogenized and dispersed – all in a single, time-efficient step.
- Fast and effective homogenization
- Excellent color ream and pigment dispersion
- Short cleaning times
- Safe operation in compliance with ATEX regulations
- Customizable batch sizes
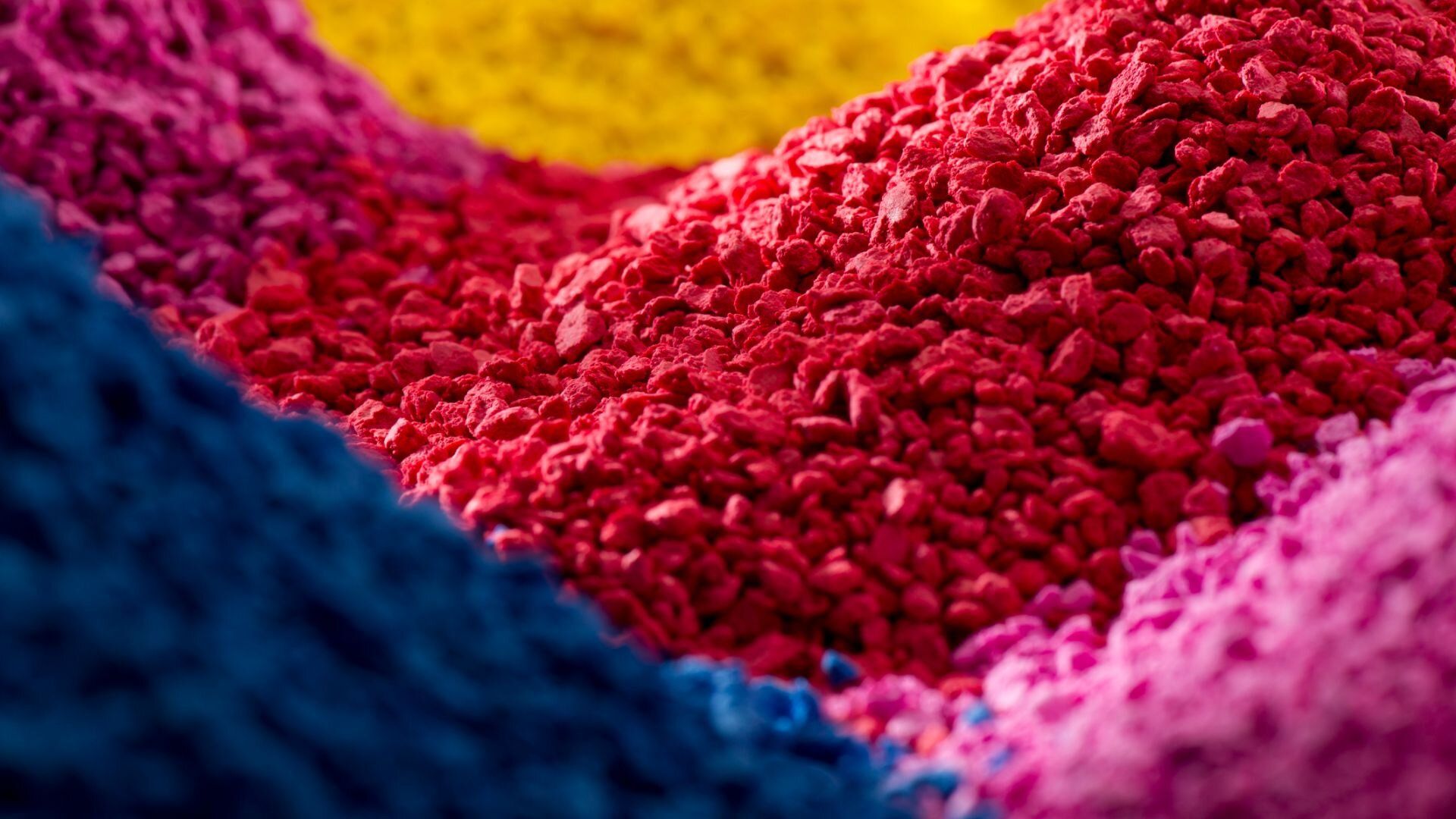
Compounds
The production of plastic components requires a variety of compounds. Depending on their specific application, plastic parts demand different compound properties. These customized mixtures are produced homogeneously and efficiently using our mixers.
- Fast and effective homogenization
- Short cleaning times
- Safe operation in compliance with ATEX regulations
- Customizable batch sizes
Benefits
Special Highlights
shorter cleaning time
No build-up, no dead zones
safe operation
Explosion-proof design according to Equipment Category 1/3 D
temperature increase per minute
Extremely low energy input
Product details
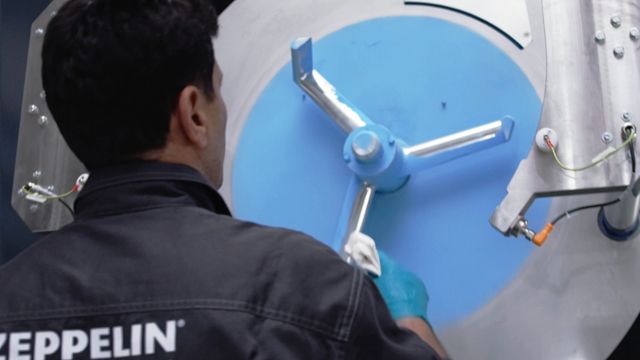
Ultrafast. Ultraclean.
The combination of a flat mixing head and wing profile tool reduces cleaning times by up to 80 % compared to conventional container mixers. The reason: all areas of the mixer are easily accessible – without the need to dismantle the mixing tool or other components.
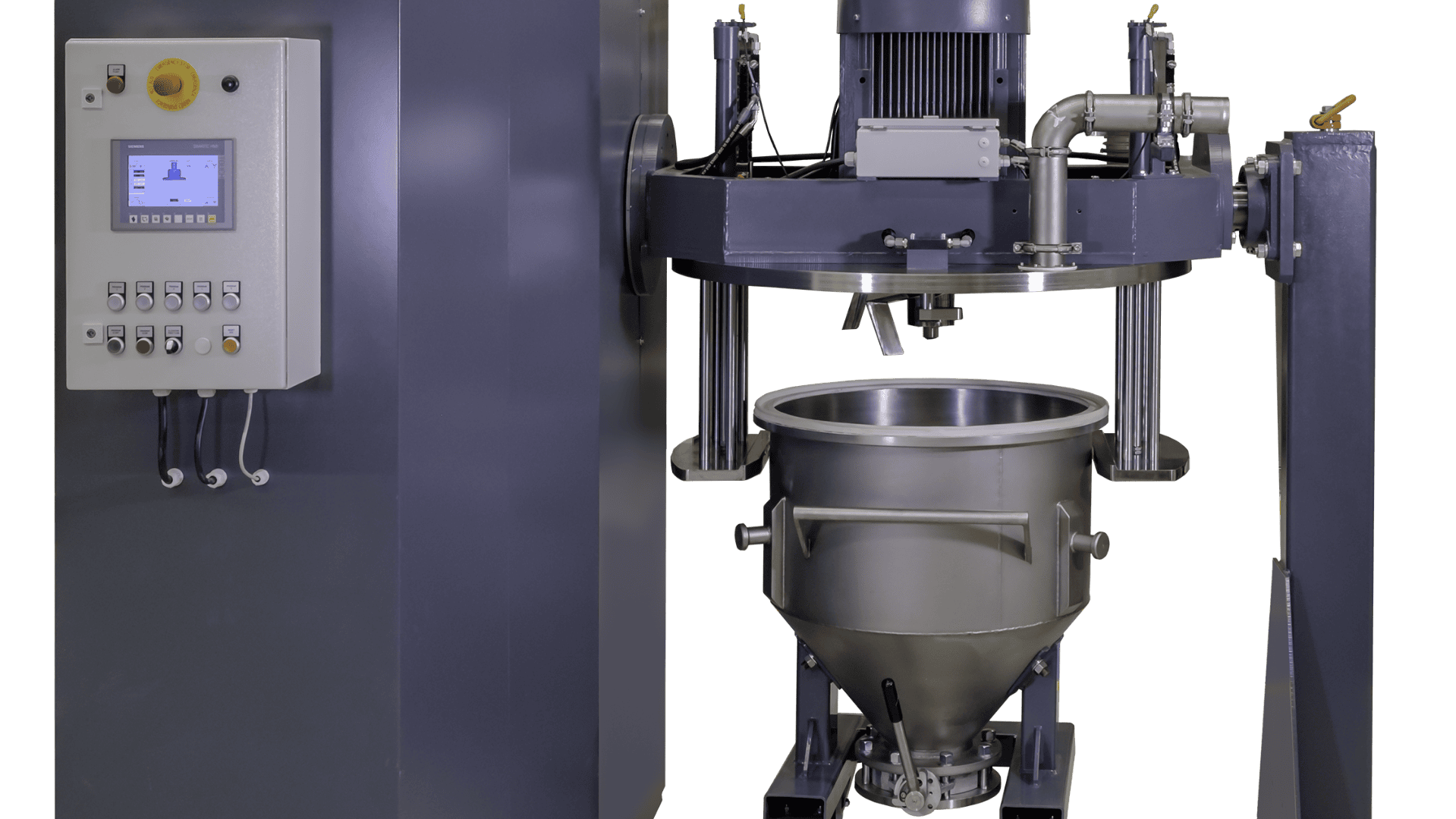
Engineered for safety
Equipped with ATEX certification and monitored grounding, our container mixers are designed to handle the demands of dust-explosive materials. The CMQ not only ensures safety but also eliminates the need for inerting in nearly all applications. That means you can focus on what matters most: achieving optimal mixing results.
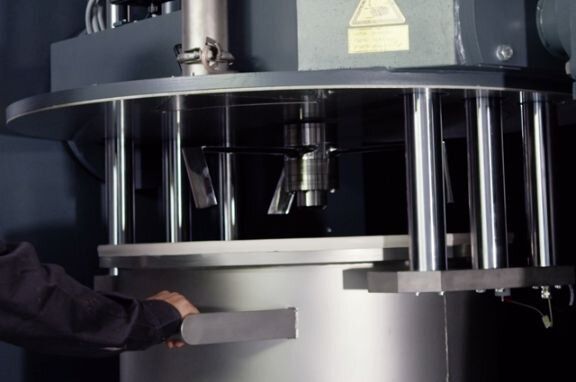
Product changeover: fast and efficient
Fast cleaning ensures ultra-short downtimes and boosts your productivity. At the same time, you remain flexible in batch size, as you can use different containers and filling volumes – tailored to your specific needs.
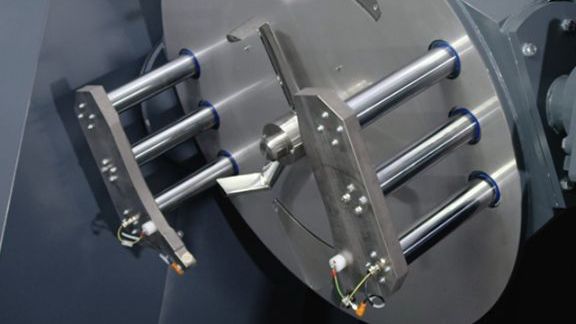
Guaranteed optimal mixing results
The patented mixing tool ensures strong color intensity through high dispersion. Its airfoil shaped mixing arms with winglets enable fast and effective homogenization – protecting your products while minimizing temperature increase to less than 2 °C per minute.
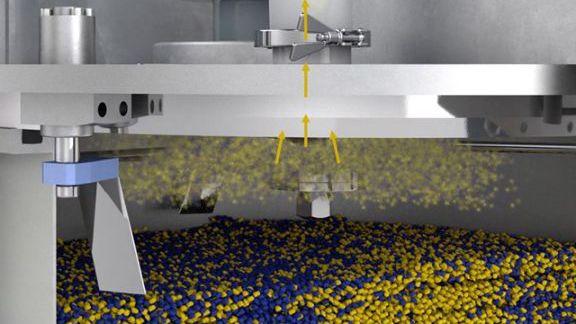
CMQ: Because cleanliness matters
During the mixing process, no dust, gases, or vapors escape – not even after the container is disconnected. This ensures a clean mixing environment while protecting plant personnel at the same time.
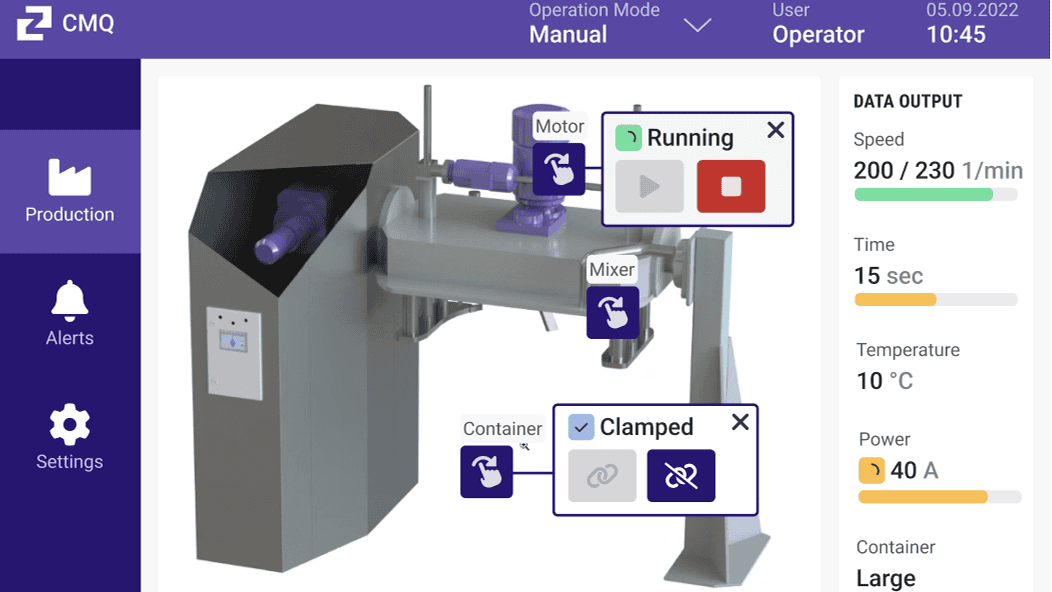
Automation
The user friendly "NAMiQ" user interface based on Siemens TIA Portal with a proven recipe management system and remote maintenance capabilities enables a safe and efficient production. The integrated control cabinet and operator panel for quick and easy installation and commissioning.
Accessories and Options
Perfect Additions for your container mixer CMQ
To ensure seamless integration and flexible use of our container mixer CMQ, we offer a range of accessories and options, including:
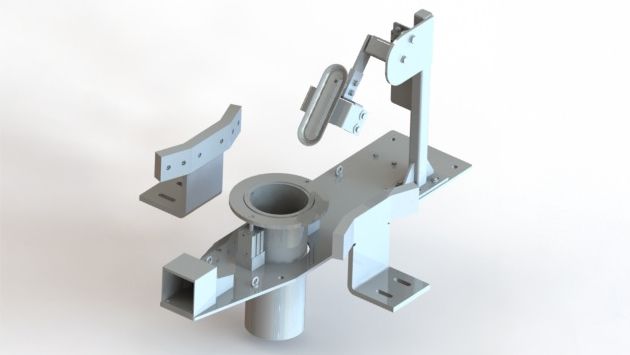
Discharge station
Discharge station for retracting or positioning the container for complete and dust-free emptying. With elastic seal for dust-free connection of discharge flap and downpipe as well as a pneumatic discharge aid for complete emptying. Many options available, such as pneumatic rotary drive, fill level indicator on the downpipe or separate control unit.
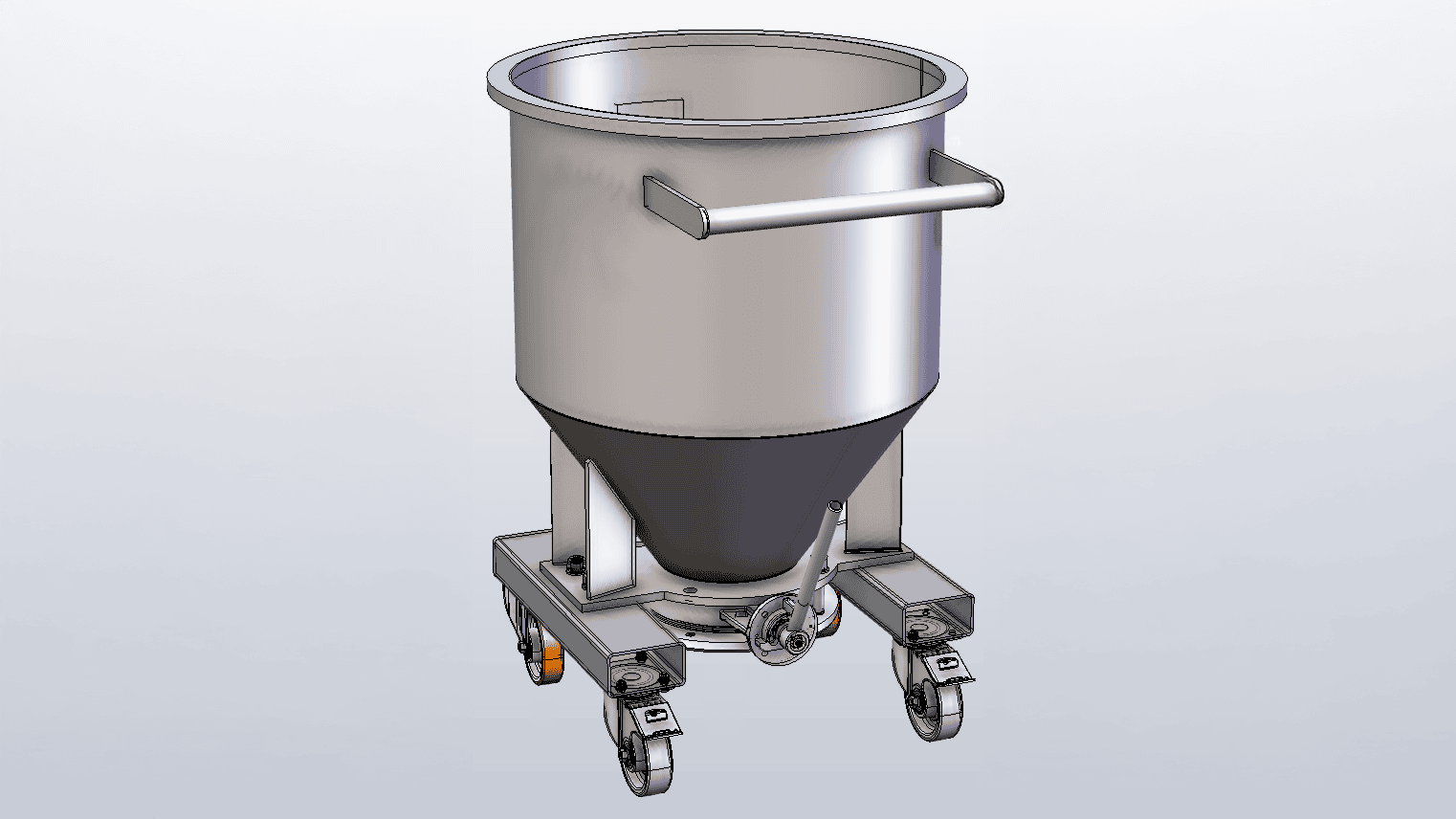
Container
Different containers with a single mixer size
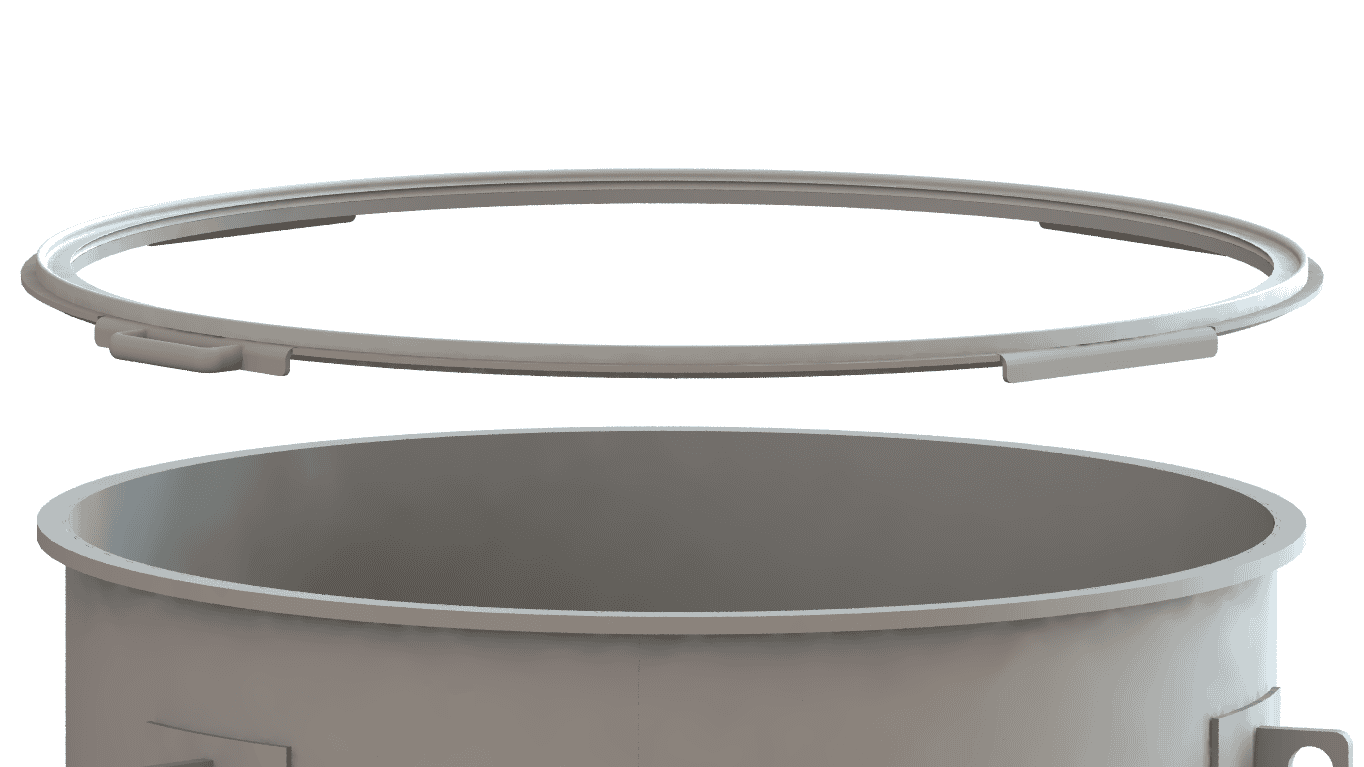
Interchangeable container seal
With an interchangeable container seal, there is no need for a seal on the container itself. The seal is replaced during a recipe change, allowing the use of existing mixing containers without a seal on the CMQ (subject to prior technical verification).
Optional liquid addition unit
Liquid addition into the product stream during the mixing process
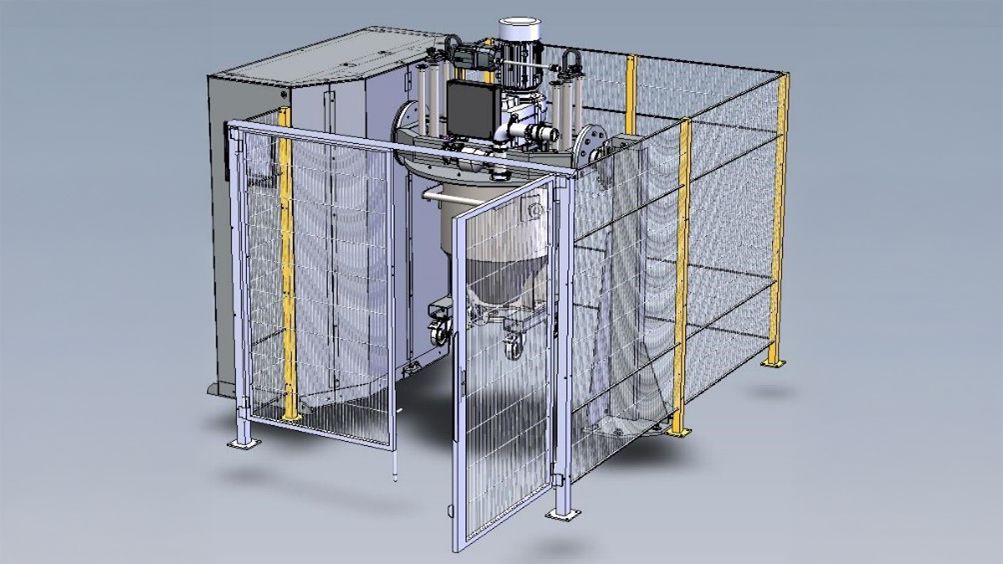
Safety fence
To protect against moving machine parts during the mixing cycle
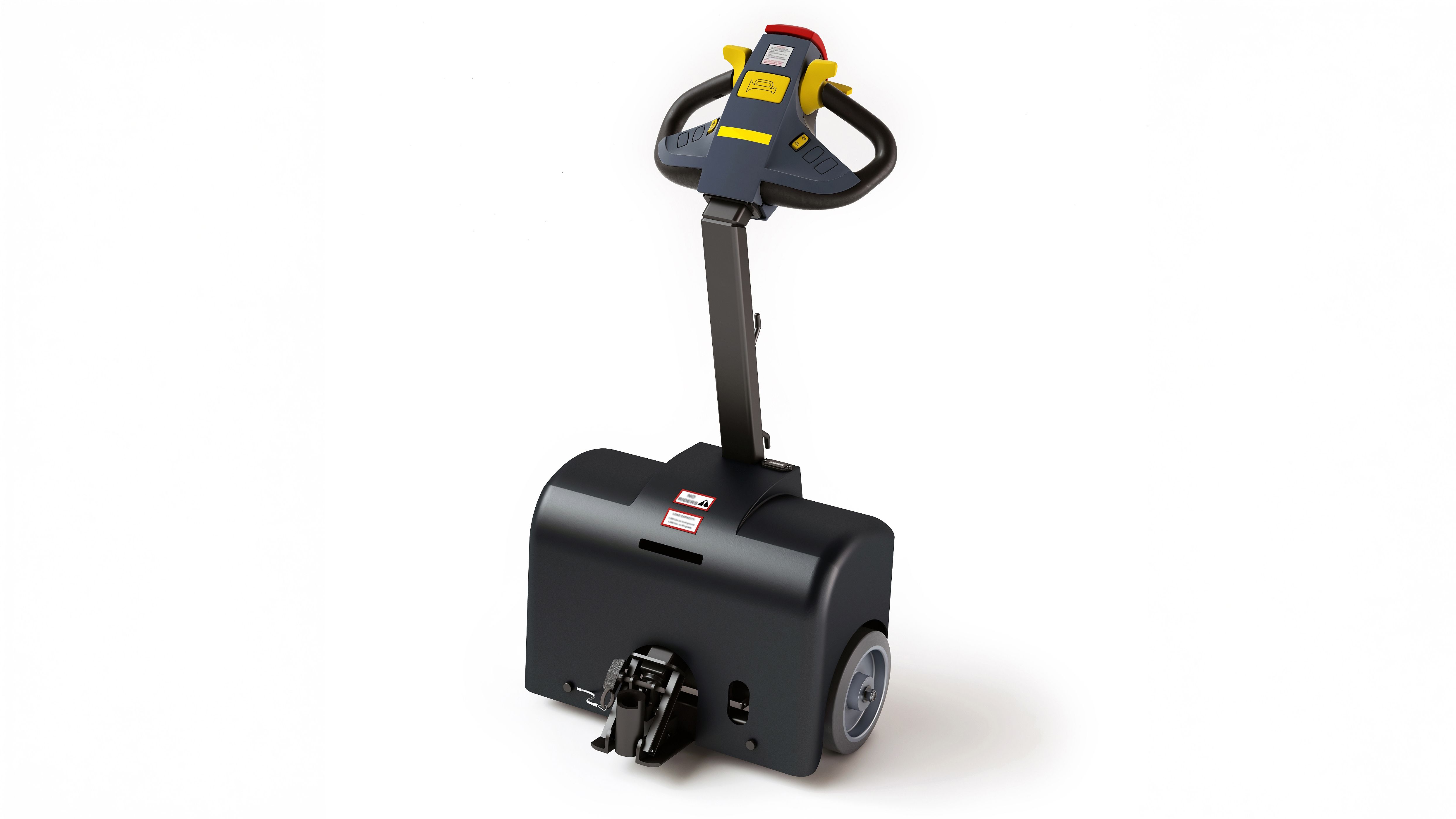
Mover
Maneuvering aid for moving the container
Need more details? Our contact person will be happy to assist you
Our Customer Services for You at a Glance
Show all Customer ServicesZeppelin Systems Technical Center
Ressources
Brochures for download
Explore more from the Zeppelin Systems portfolio
Products
© 2025 Zeppelin Systems GmbH