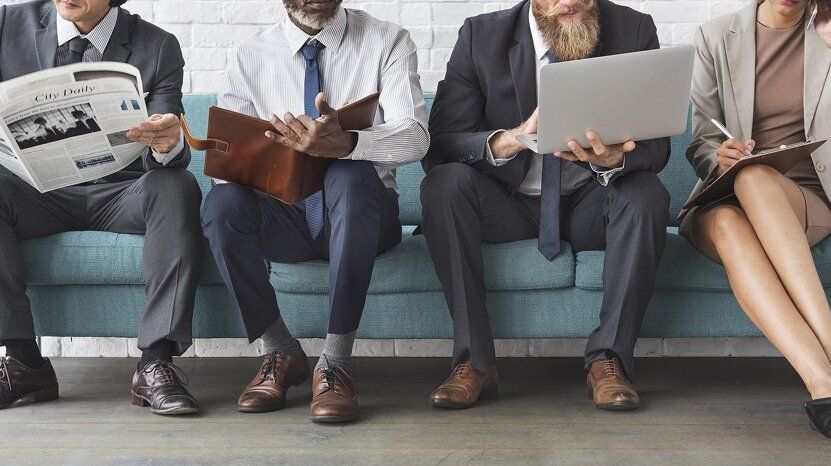
Press releases & News
Stay informed!
Latest news and press releases
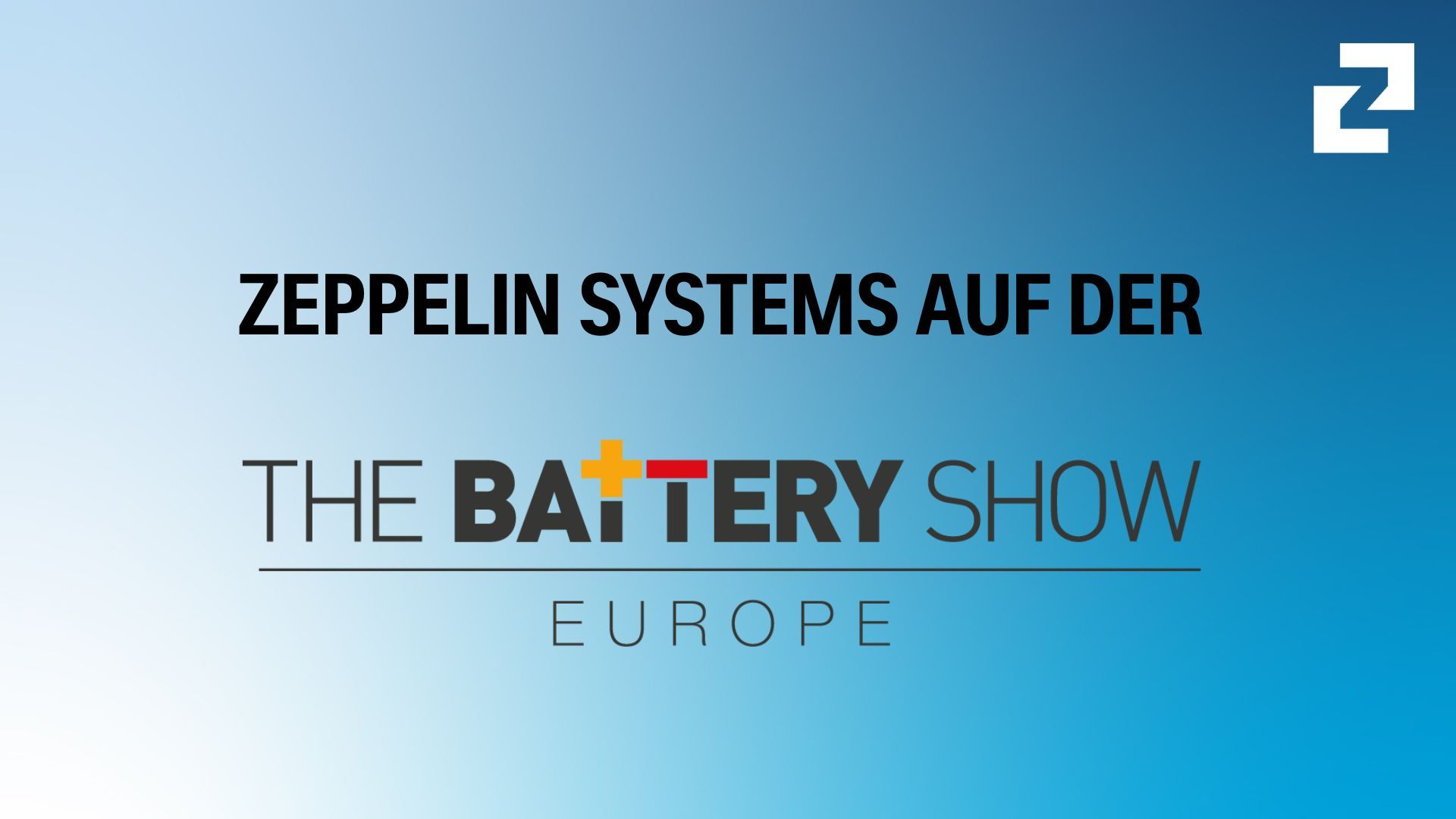
Zeppelin Systems presents its extensive solutions portfolio for battery mass production at Battery Show Europe 2025
As a global plant engineering company, Zeppelin Systems is a single source for supplying integrated complete solutions for the efficient processing of raw materials. The company will attend Battery Show Europe in Stuttgart to showcase its expertise i...
Continue reading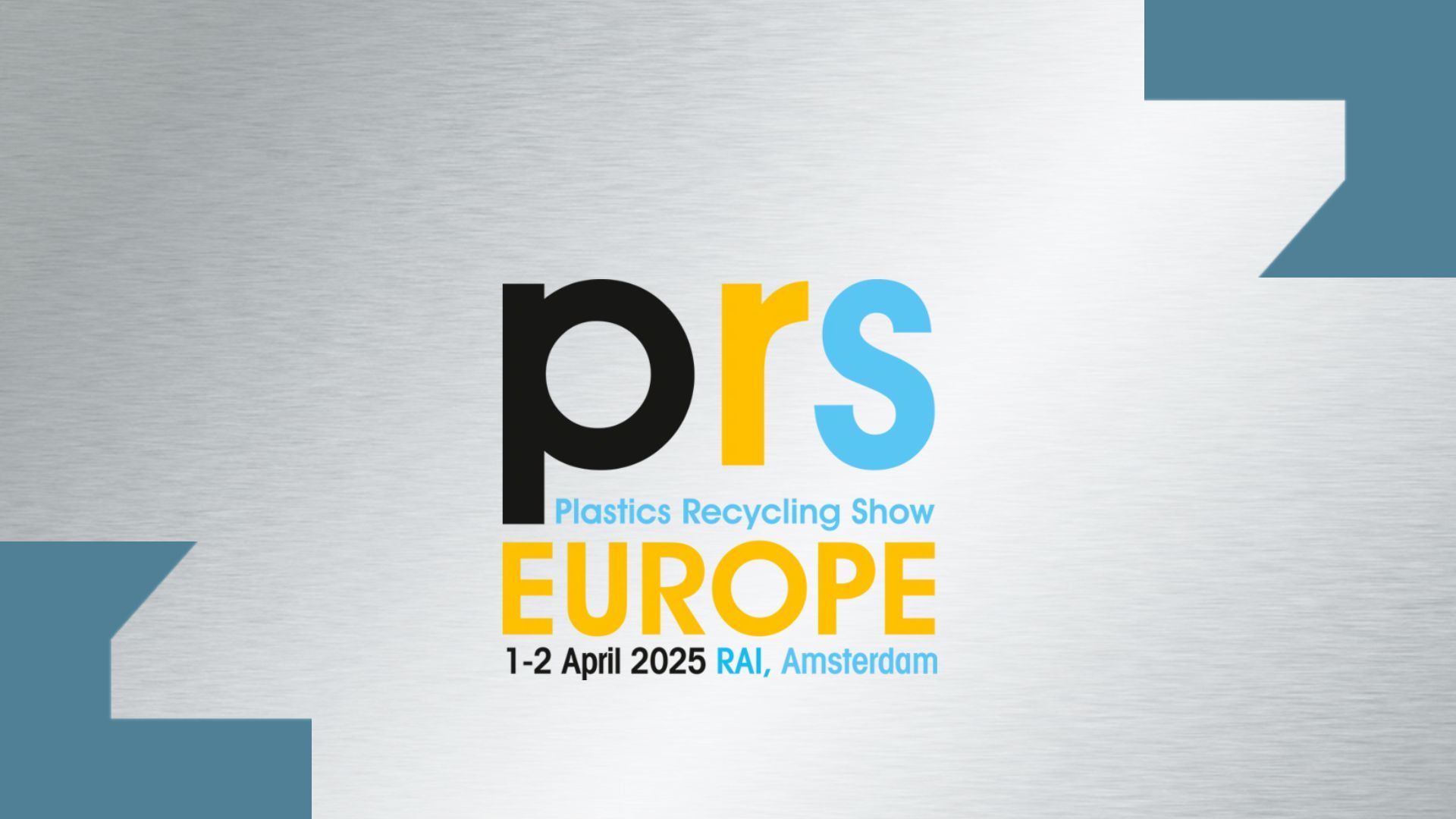
Zeppelin Systems presents comprehensive recycling solutions for plastics at PRSE 2025 in Amsterdam
How do you start recycling plastics? At the PRSE trade fair in Amsterdam on April 1 - 2, the experienced plant engineering expert Zeppelin Systems will present innovative solutions for plastics recycling and also showcase a laboratory system for deod...
Continue reading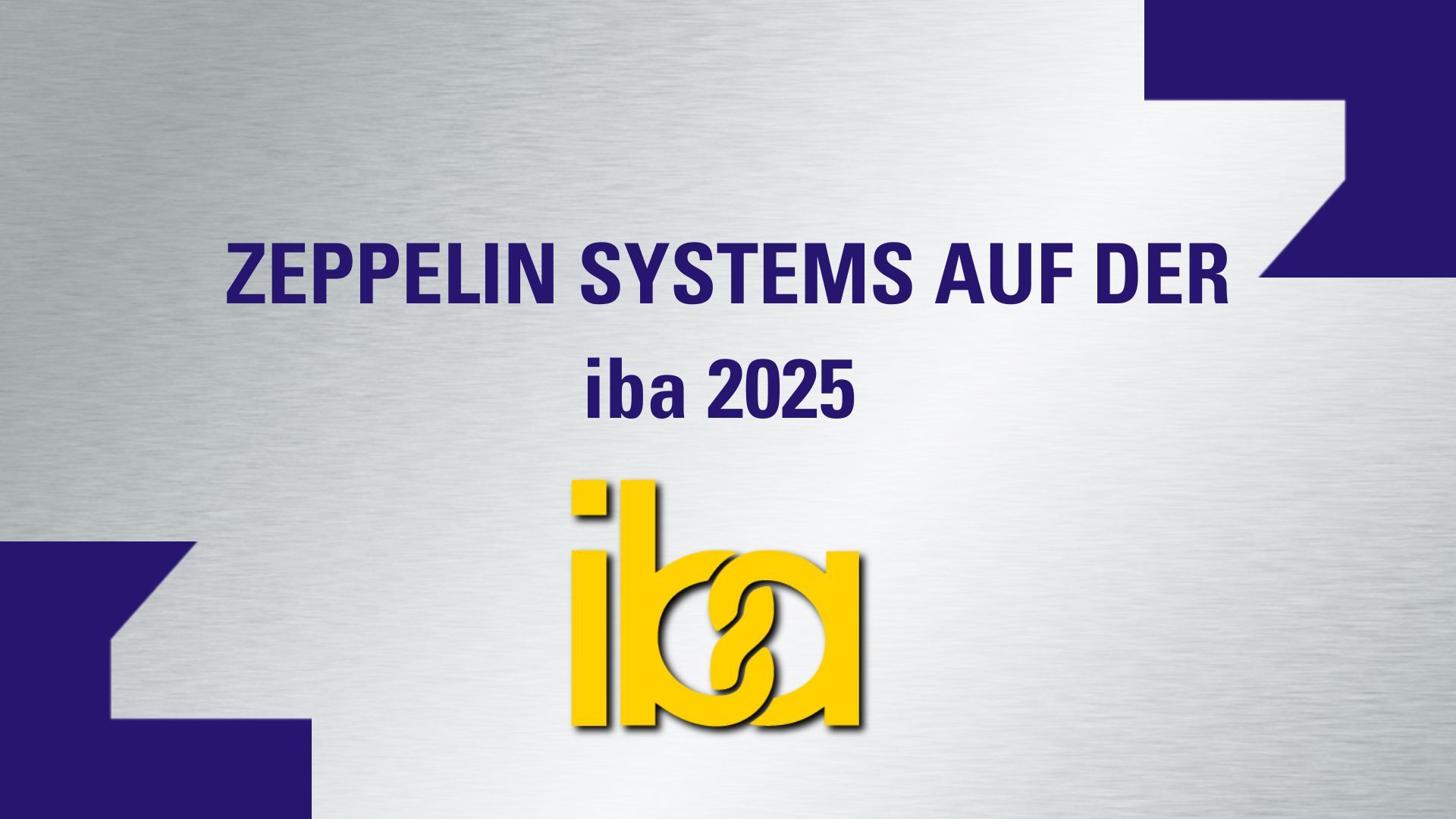
Zeppelin Systems is presenting at iba 2025
Zeppelin Systems is showcasing its industry expertise in food systems at iba, the world’s leading trade fair for the bakery, confectionery and snacks industries. The focus of this year's trade fair participation is a combination of three topics: redu...
Continue reading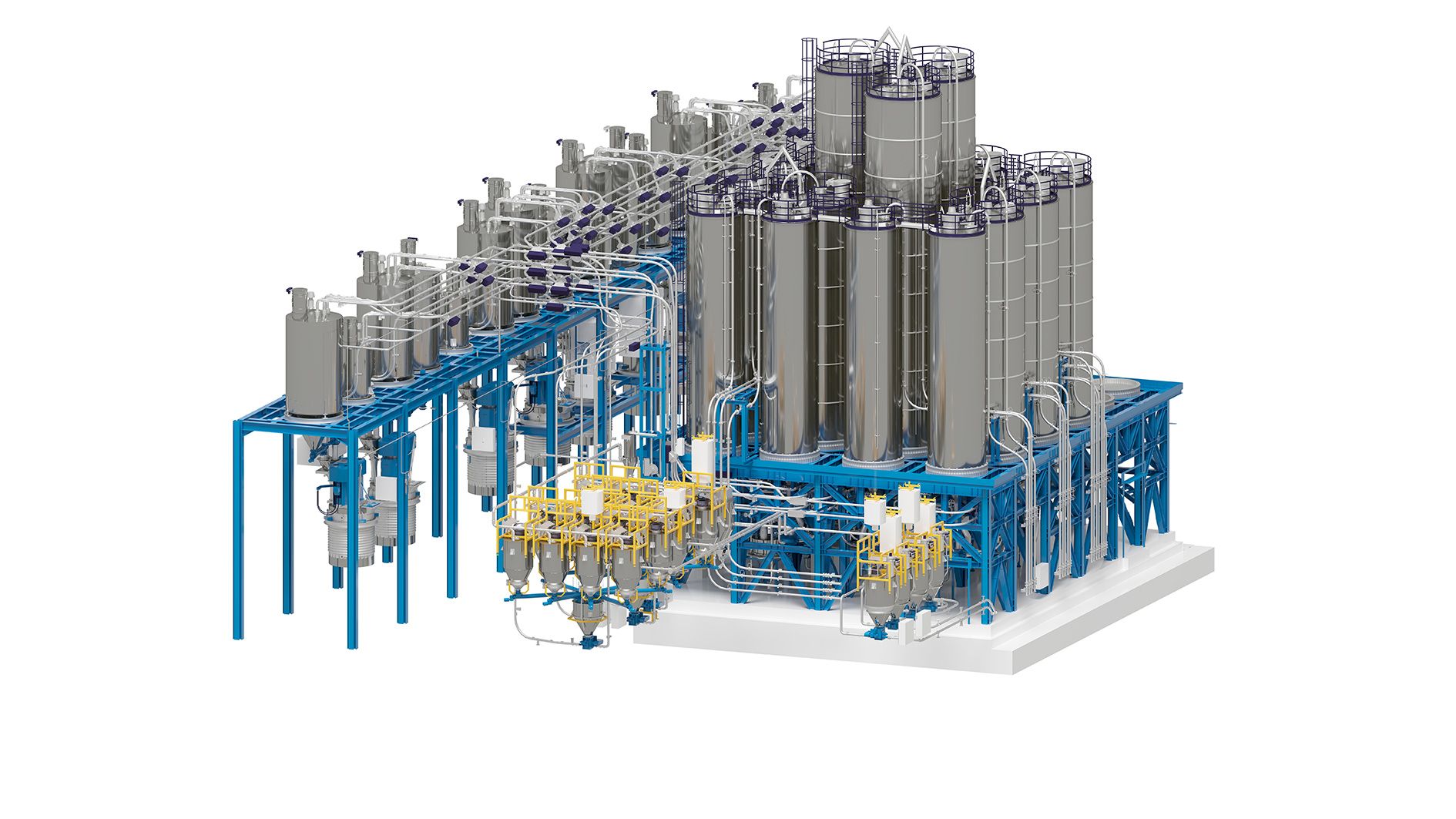
Zeppelin Systems to present at the European Coatings Show 2025
Zeppelin Systems will be demonstrating its industry expertise at the leading trade fair for the international paint and coatings industry, the European Coatings Show (ECS). This year, the focus of the trade fair presentation will be on a process mixe...
Continue reading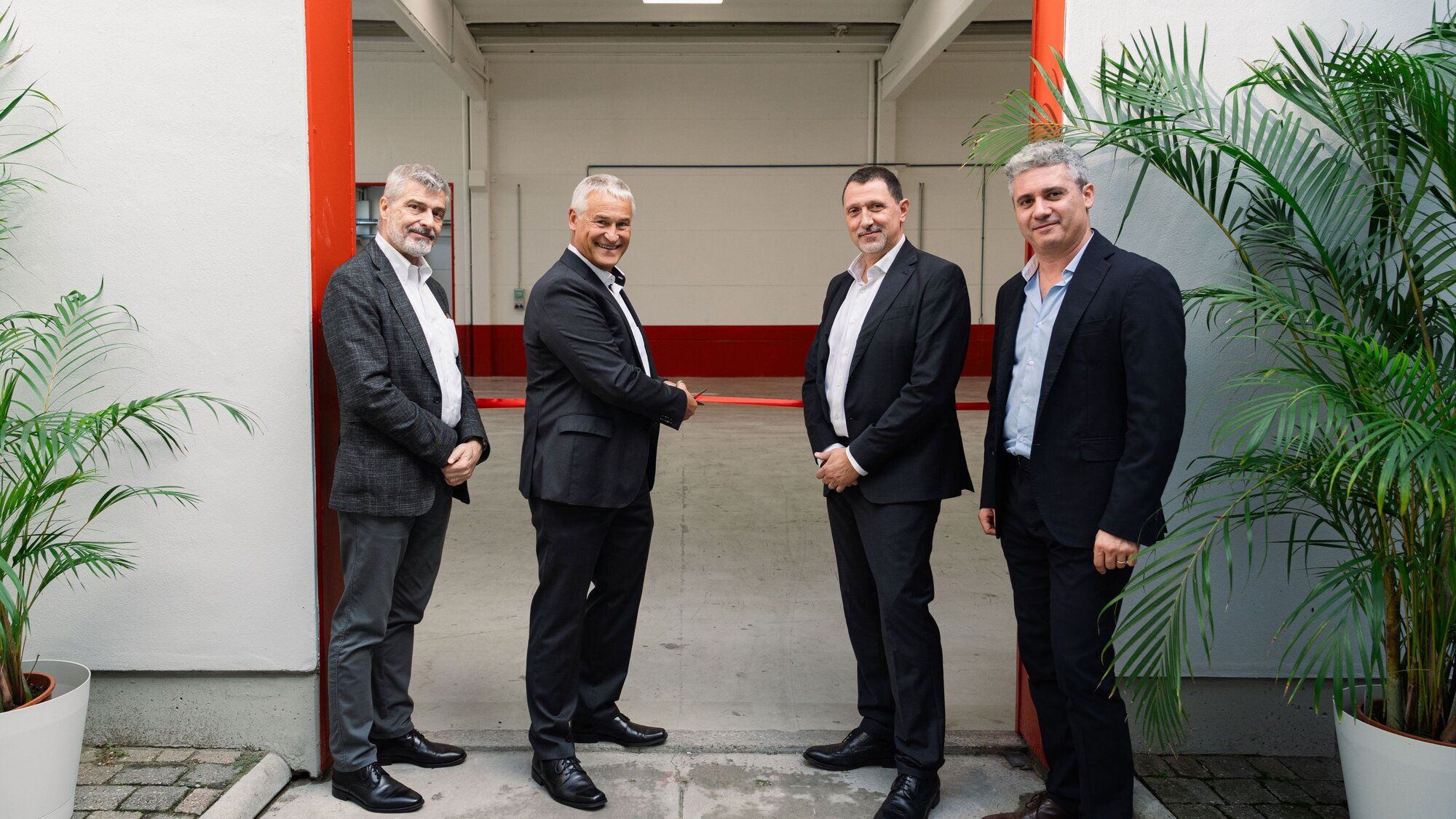
Zeppelin Systems strengthens its presence in Italy
Together with Nuova Ciba, which was acquired in 2018, Zeppelin Systems has been active in the Italian market for many years and is now reaffirming its commitment with the inauguration and opening of new, modern premises at the competence centre in Re...
Continue reading
Zeppelin Systems presents innovative solutions for battery mass production at the Batteries Event in Lyon
As leading expert in the efficient processing of raw materials, plant manufacturer Zeppelin Systems will be presenting pioneering high-performance mixers, innovative mixing processes and efficient material conveying and dosing systems for the product...
Continue reading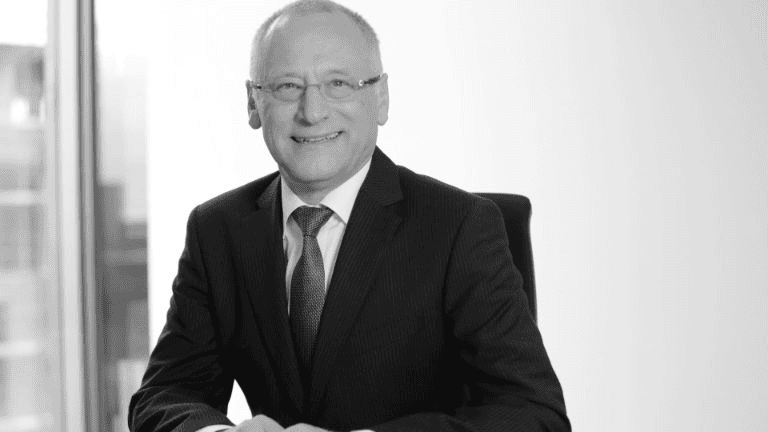
Zeppelin Systems mourns the loss of former Managing Director Rochus Hofmann
After almost 20 years at the helm of the company, plant manufacturer Zeppelin Systems did not bid farewell to Rochus Hofmann until July 2023, when he took his well-deserved retirement. On September 8, 2024, the much-loved and esteemed CEO passed away...
Continue reading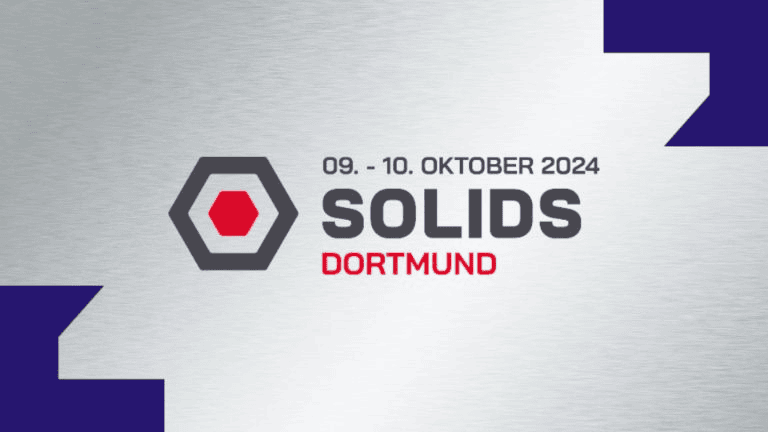
Zeppelin Systems hacks something out at the Solids 2024 trade fair
The trade fair for granulate, powder and bulk solids technologies in Dortmund, Germany, has come up with something special this year to inspire the international audience: The ‘Bulk Masters’ hackathon will start on October 8 2024 - the new hands-on e...
Continue reading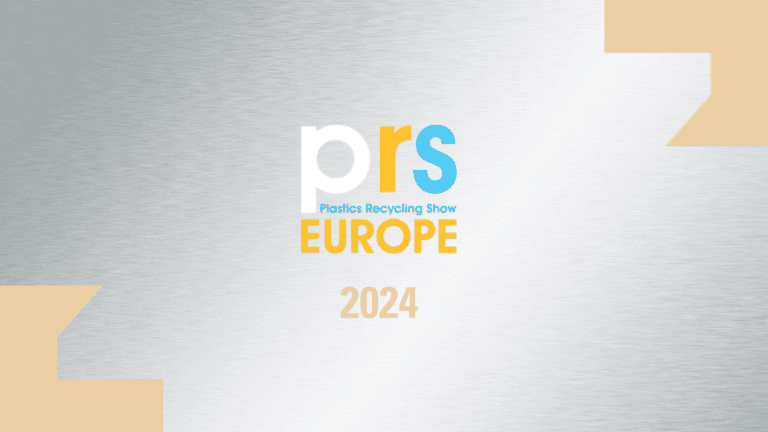
Zeppelin Systems presents comprehensive plastics recycling solutions at PRSE 2024 in Amsterdam
A new EU directive has set a requirement that, by the end of 2025, around 65% by weight of all packaging waste in Europe must be recycled. And by 2030 at the latest, this level will go up to at least 70% by weight. With its considerable experience in...
Continue reading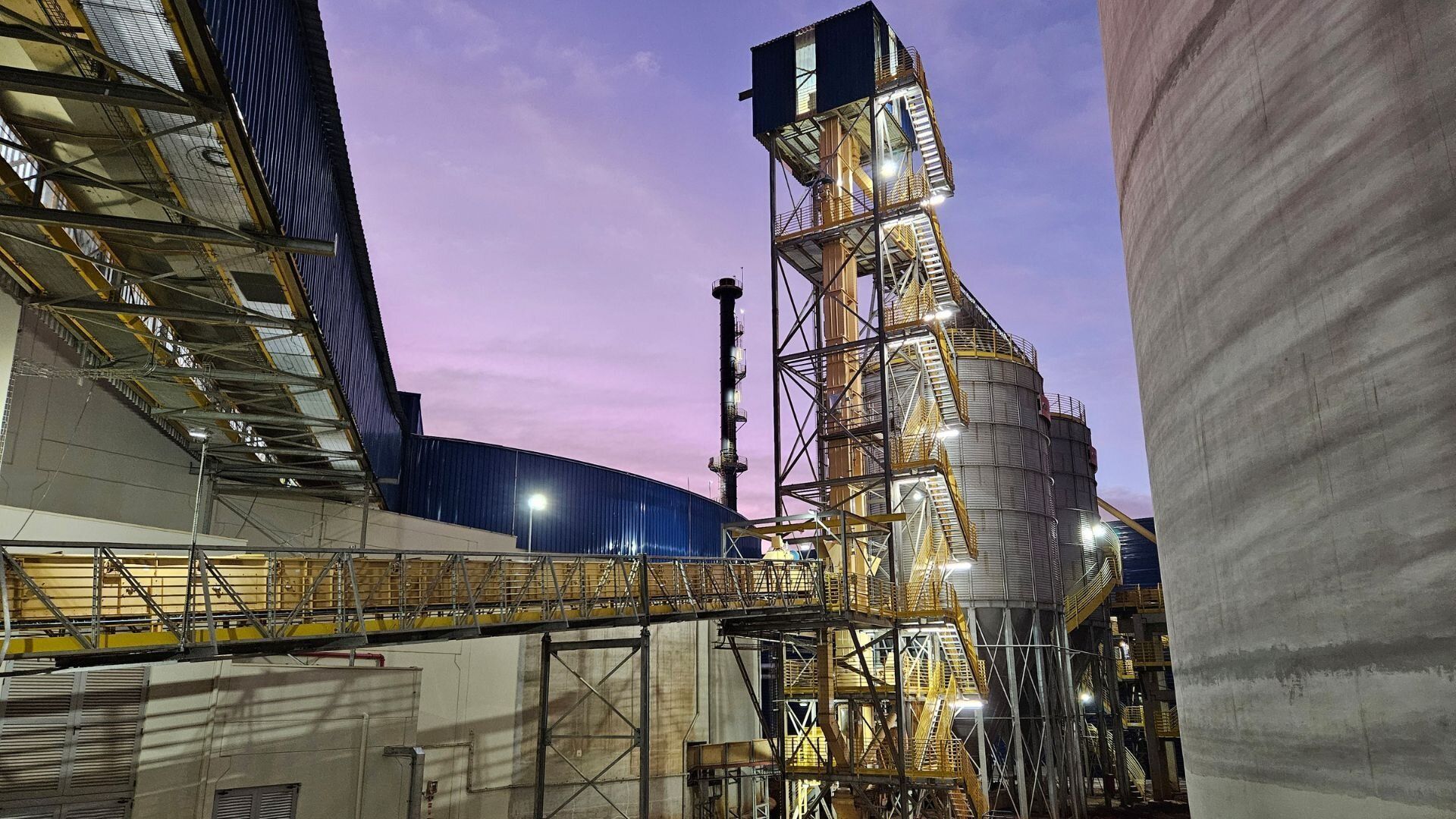
Zeppelin Systems celebrates turnkey handover of a malting plant full of superlatives in Brazil
Zeppelin Systems, a global system builder and solution provider, was tasked with planning, constructing and commissioning the world’s largest (built in one piece) malting plant in Ponta Grossa (Campos Gerais region in Brazil). As a reliable engineeri...
Continue readingPress contact
Zeppelin Systems Company
Learn more about Zeppelin Systems
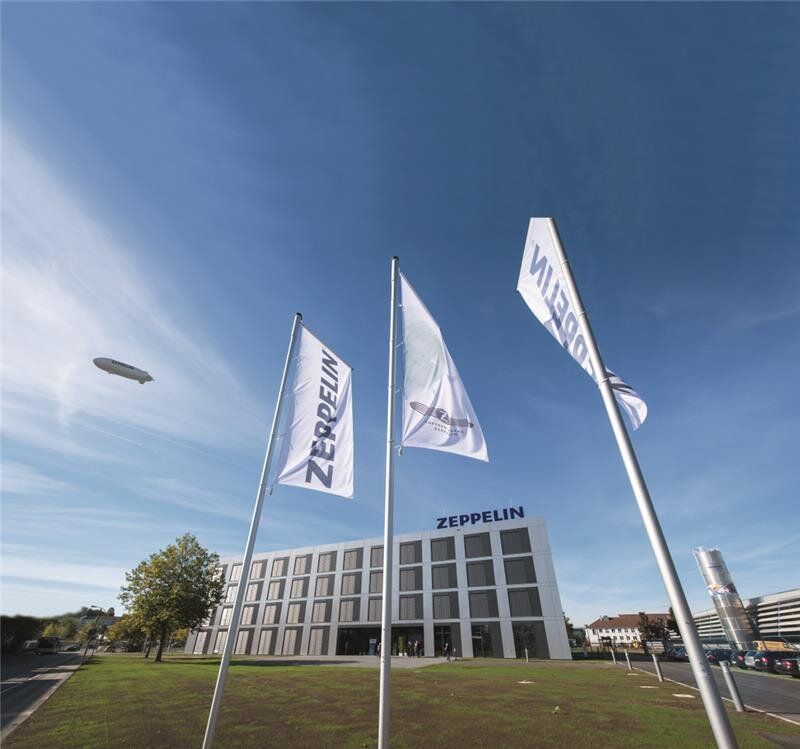
About Zeppelin Systems
Learn more about plant engineering and solutions provider Zeppelin Systems!
Go to about us
Facts & Figures about plant engineering company Zeppelin Systems
Key information about Zeppelin Systems at a glance.
Go to facts & figures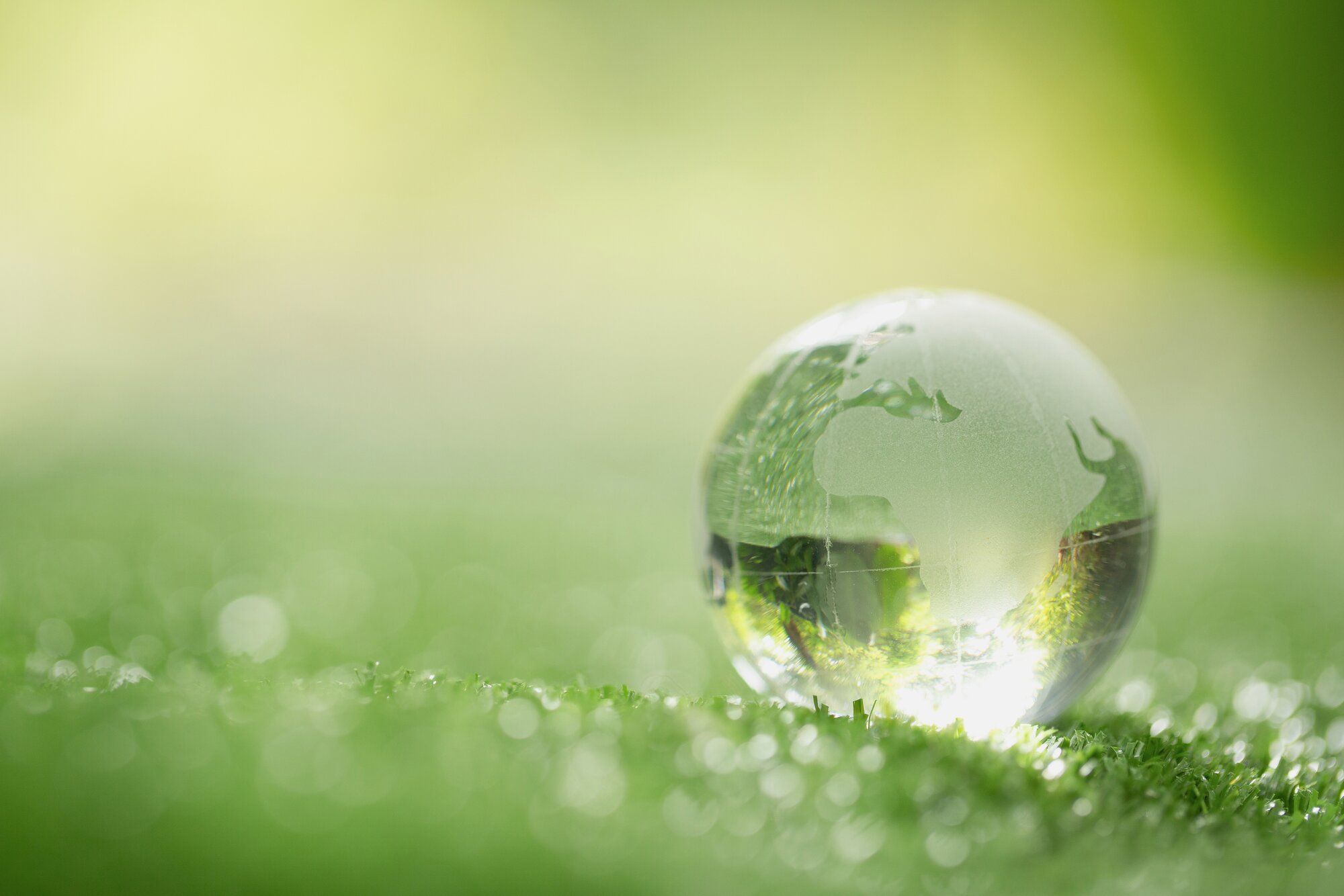
Sustainability at Zeppelin Systems
Our responsibility as a foundation-owned company.
Go to sustanability initiatives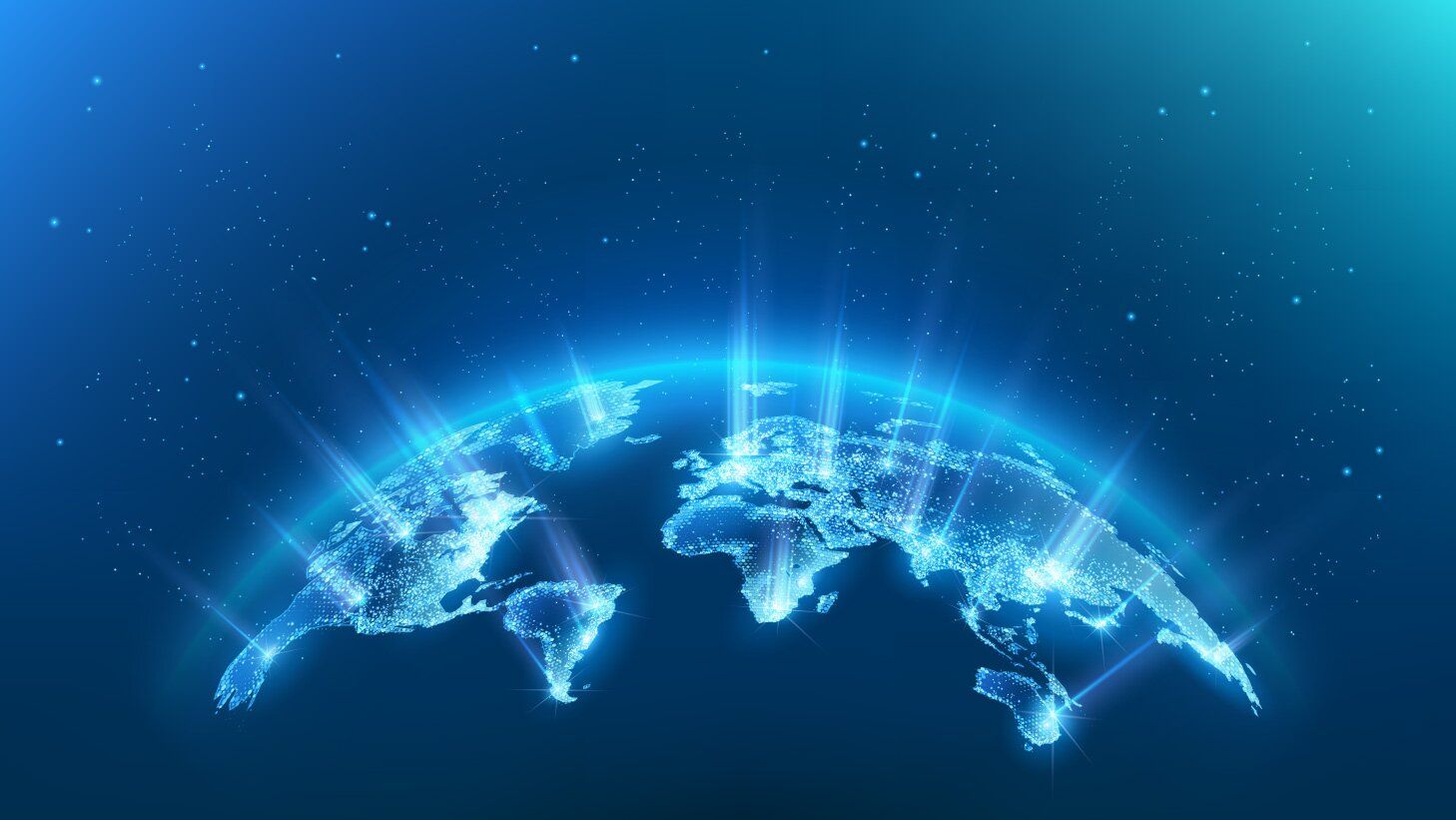
Zeppelin Systems worldwide – Contact & Locations
Discover more about the plant engineering and solutions provider Zeppelin Systems!
Go to our contact & locations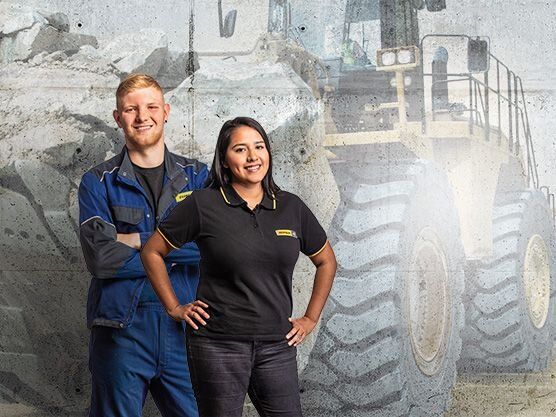
Career at Zeppelin Systems
We are always looking for talented individuals. Visit our careers portal to learn more
Go to careers portal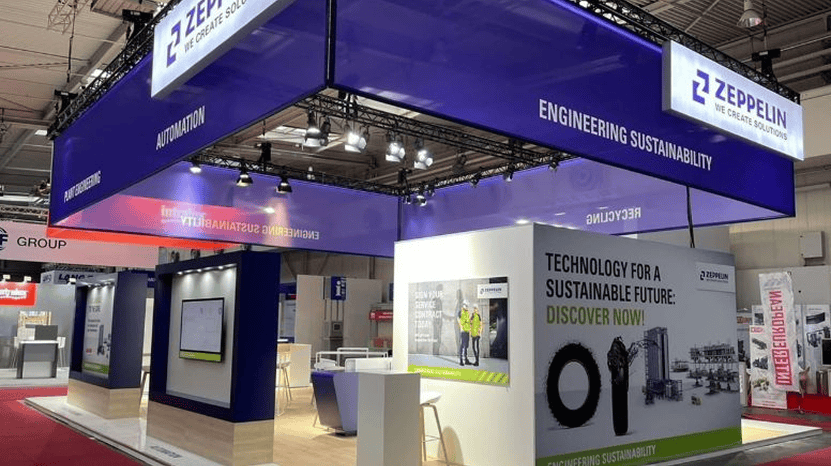
Trade Fairs & Events
Zeppelin Systems is represented at all major trade fairs worldwide within its industries – we look forward to welcoming you at the next event.
Go to trade fairs & events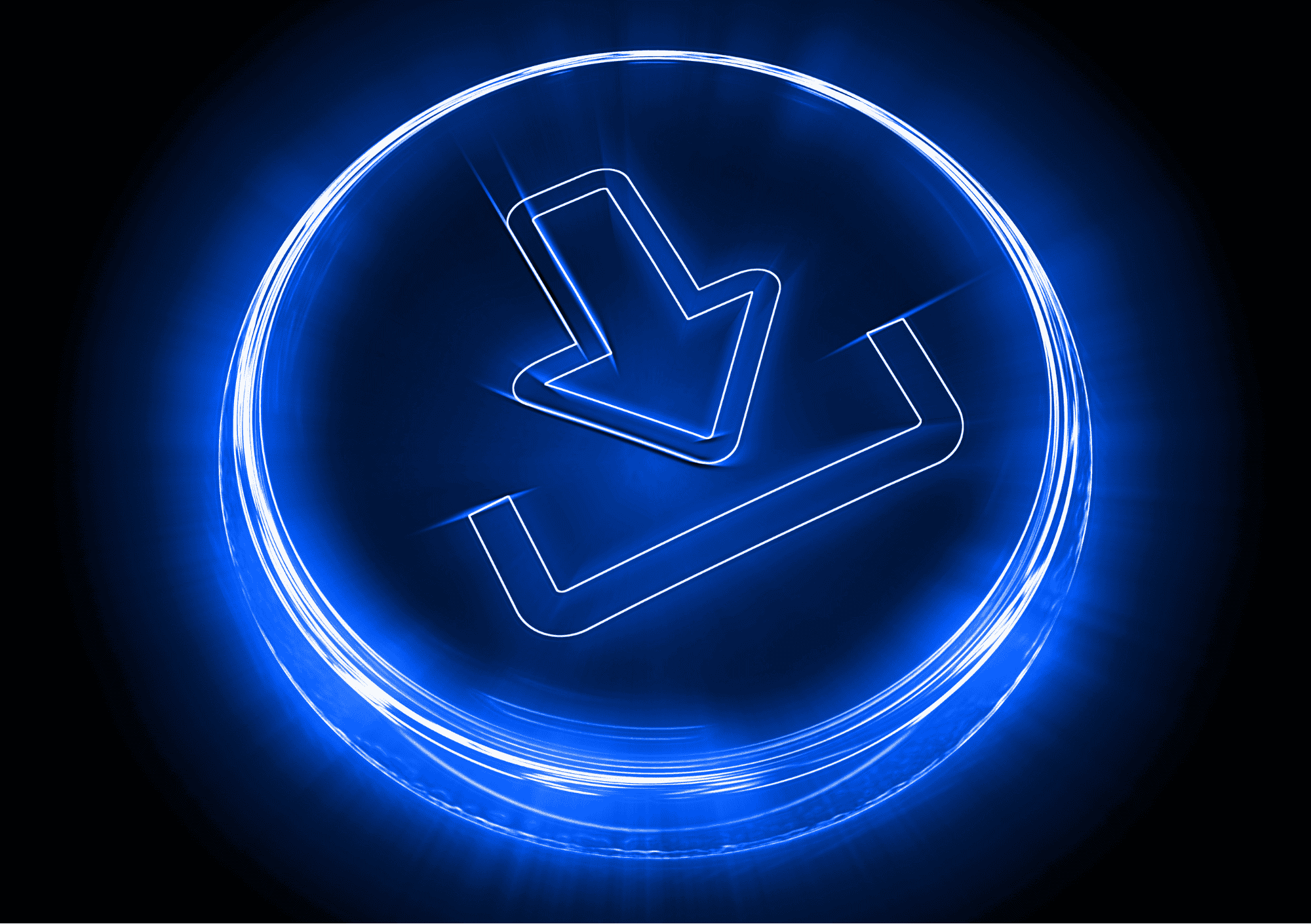
Downloads
Here you will find a wide range of brochures and data sheets to learn more about our products and services.
Go to downloads© 2025 Zeppelin GmbH