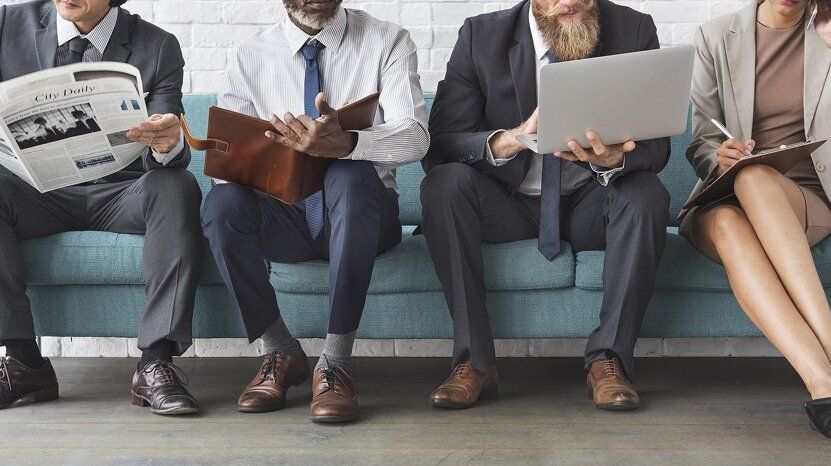
Pressemitteilungen & News
Bleiben Sie informiert!
Aktuelle Nachrichten und Pressemitteilungen
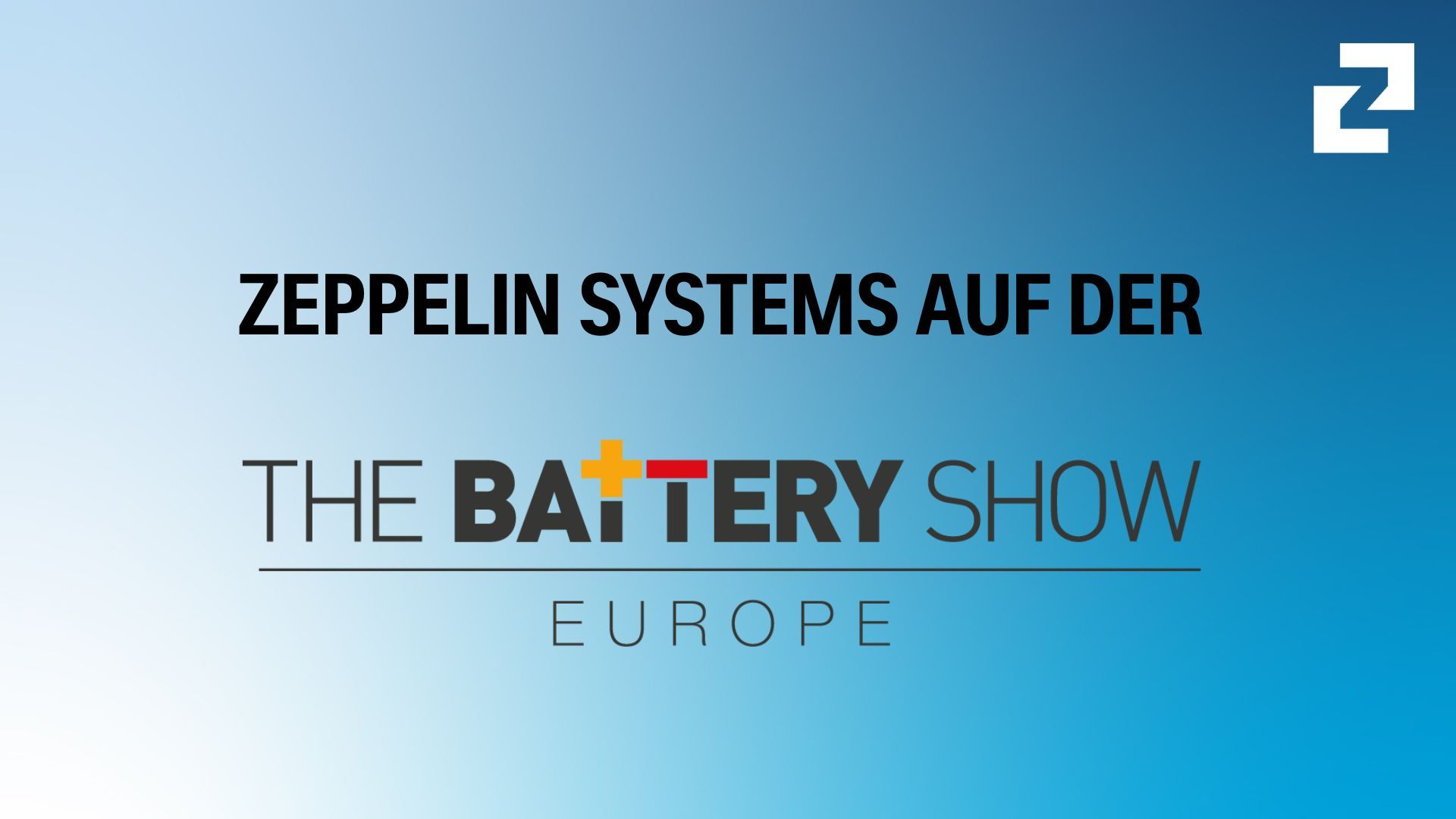
Zeppelin Systems präsentiert sein breites Lösungsportfolio für die Batteriemassenproduktion auf der Battery Show Europe 2025
Zeppelin Systems bietet als globaler Anlagenbauer integrierte Komplettlösungen für die effiziente Aufbereitung von Rohstoffen aus einer Hand. Auf der Battery Show Europe in Stuttgart zeigt das Unternehmen seine Expertise im Bereich Batteriemassenprod...
Weiterlesen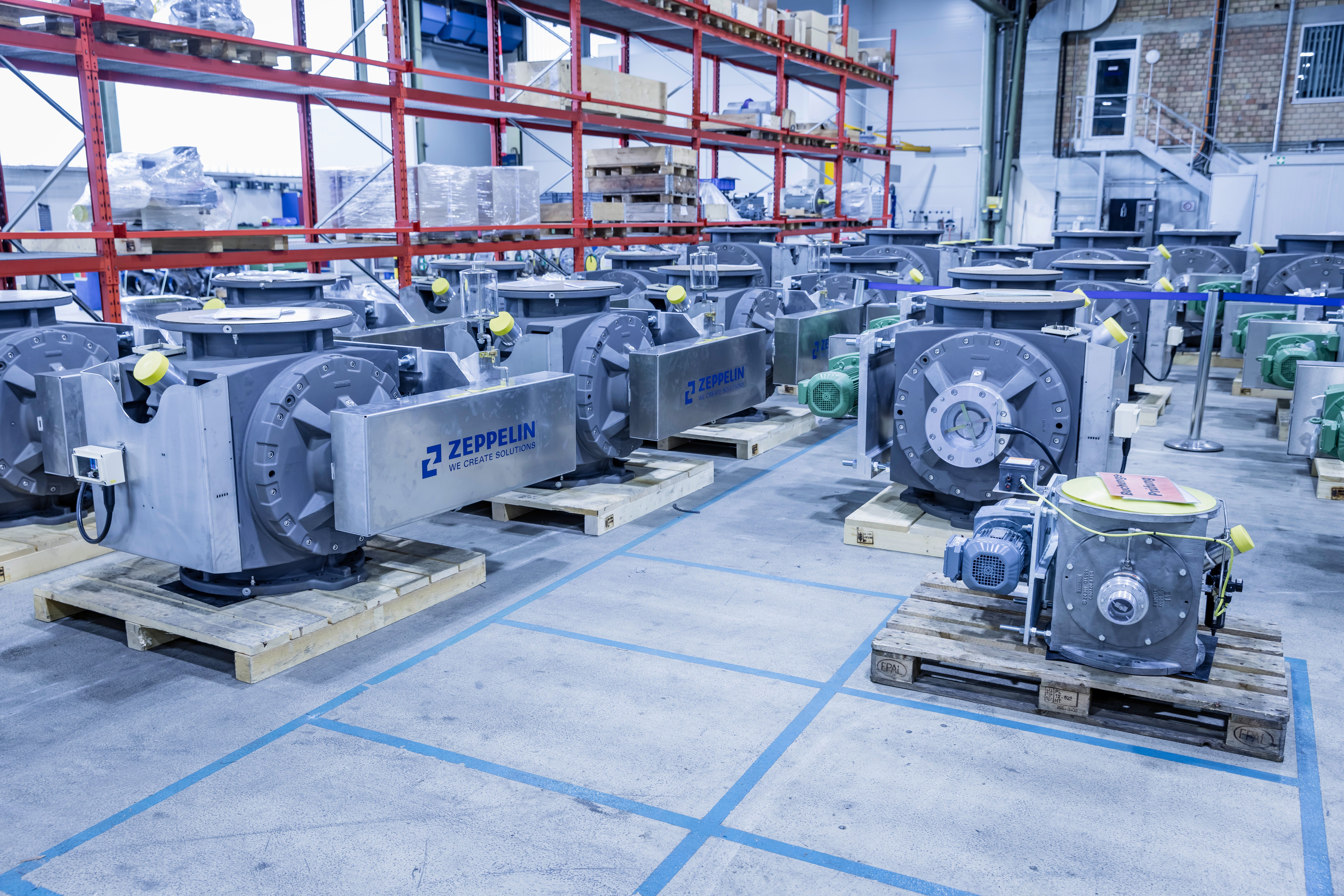
Zeppelin Systems zeigt bei „Lange Nacht der Technik & Innovation“ nachhaltige Lösungen im Anlagenbau
Im Rahmen der diesjährigen „Langen Nacht der Technik & Innovation“ in Friedrichshafen heißt Zeppelin Systems große und kleine Technikinteressierte willkommen. Am Freitag, den 16. Mai 2025 können sie sich von 17 bis 22 Uhr auf dem Gelände des Unterneh...
Weiterlesen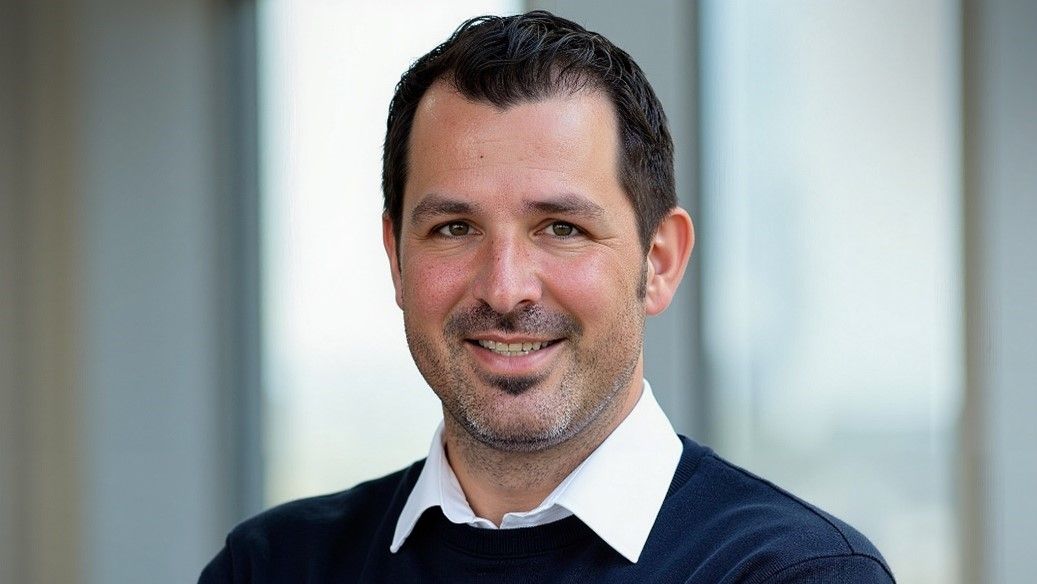
Zeppelin Konzern besetzt Vorsitz der Geschäftsführung der Zeppelin Systems GmbH neu
Sascha Stiller übernimmt zum 1. April 2025 den Vorsitz der Geschäftsführung der Zeppelin Systems GmbH sowie die Leitung der Strategischen Geschäftseinheit (SGE) Anlagenbau. Damit verantwortet Stiller auch alle weltweiten Tochtergesellschaften. Hubert...
Weiterlesen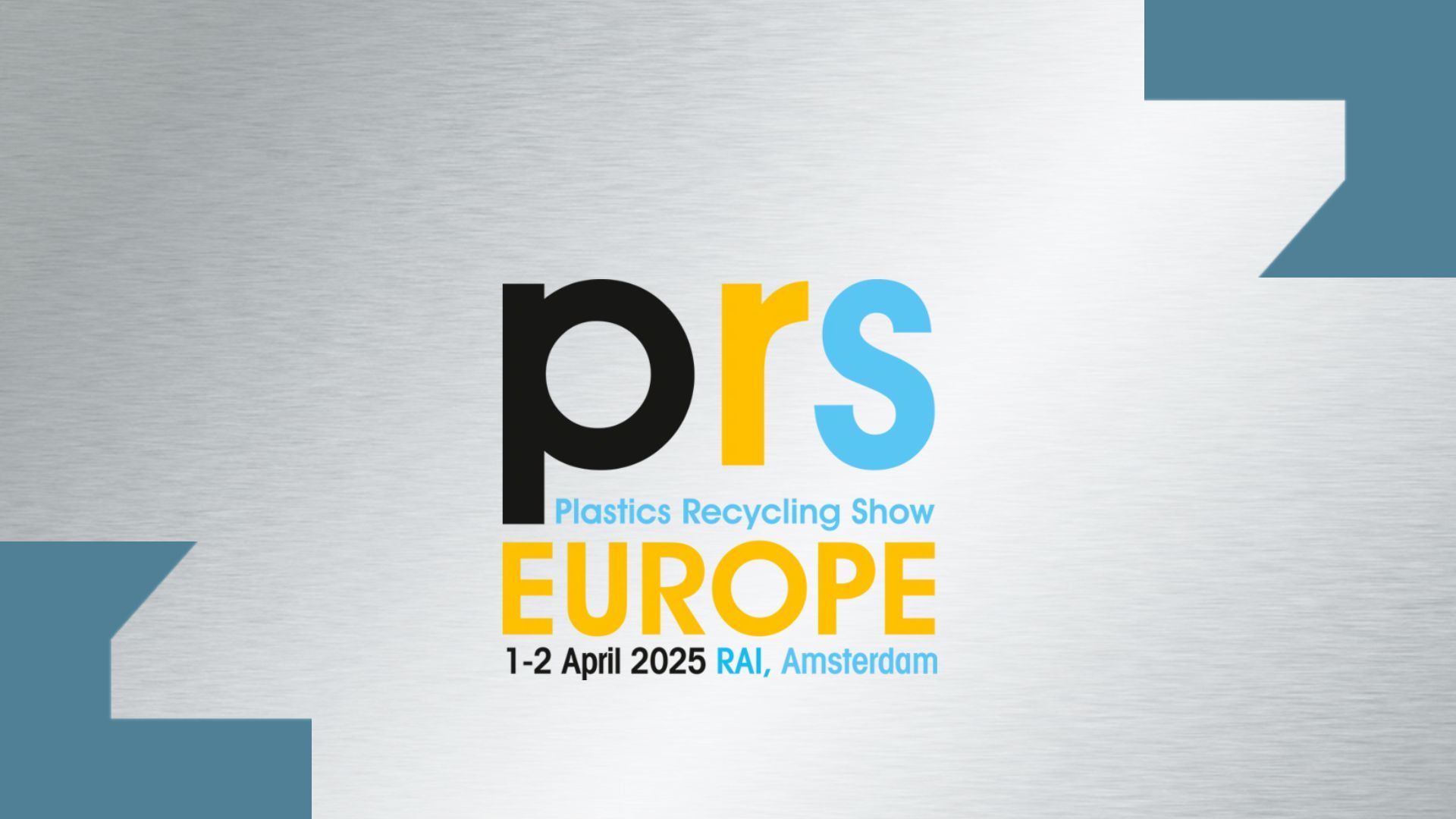
Zeppelin Systems zeigt ganzheitliche Recycling-Lösungen für Kunststoffe auf der PRSE 2025 in Amsterdam
Wie findet man den Einstieg in das Recycling von Kunststoffen? Der erfahrene Anlagenbauer Zeppelin Systems präsentiert auf der Fachmesse PRSE in Amsterdam vom 1. bis 2. April nicht nur innovative Lösungen für das Kunststoffrecycling, sondern unter an...
Weiterlesen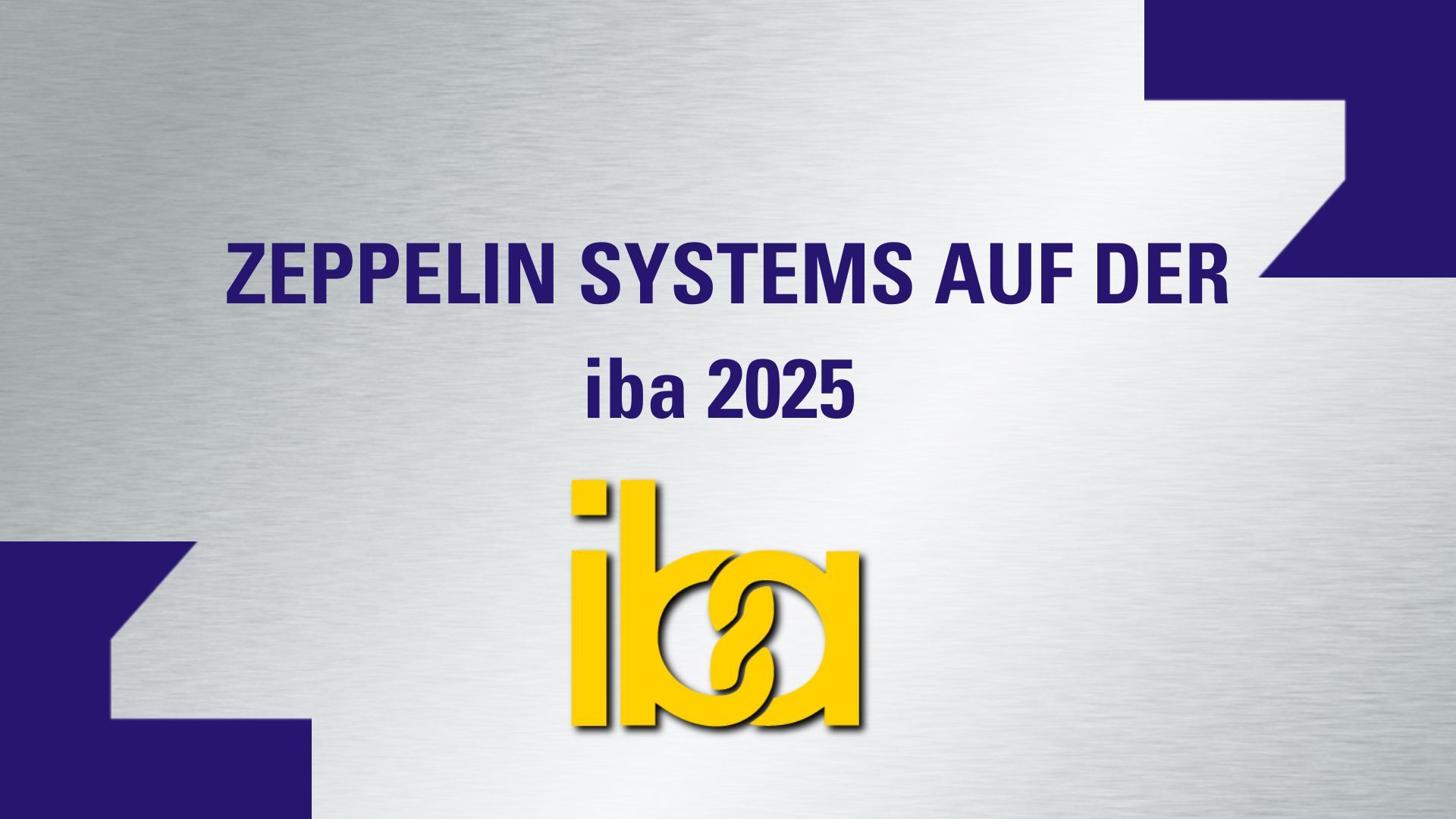
Zeppelin Systems präsentiert sich auf der iba 2025
Zeppelin Systems zeigt auf der der iba, der weltweit führenden Weltmesse für die Branchen Bäckerei, Konditorei und Snacks, seine Branchenexpertise für Lebensmittelanlagen. Im Mittelpunkt des Messeauftritts steht diesmal ein Dreiklang aus Kosten- und ...
Weiterlesen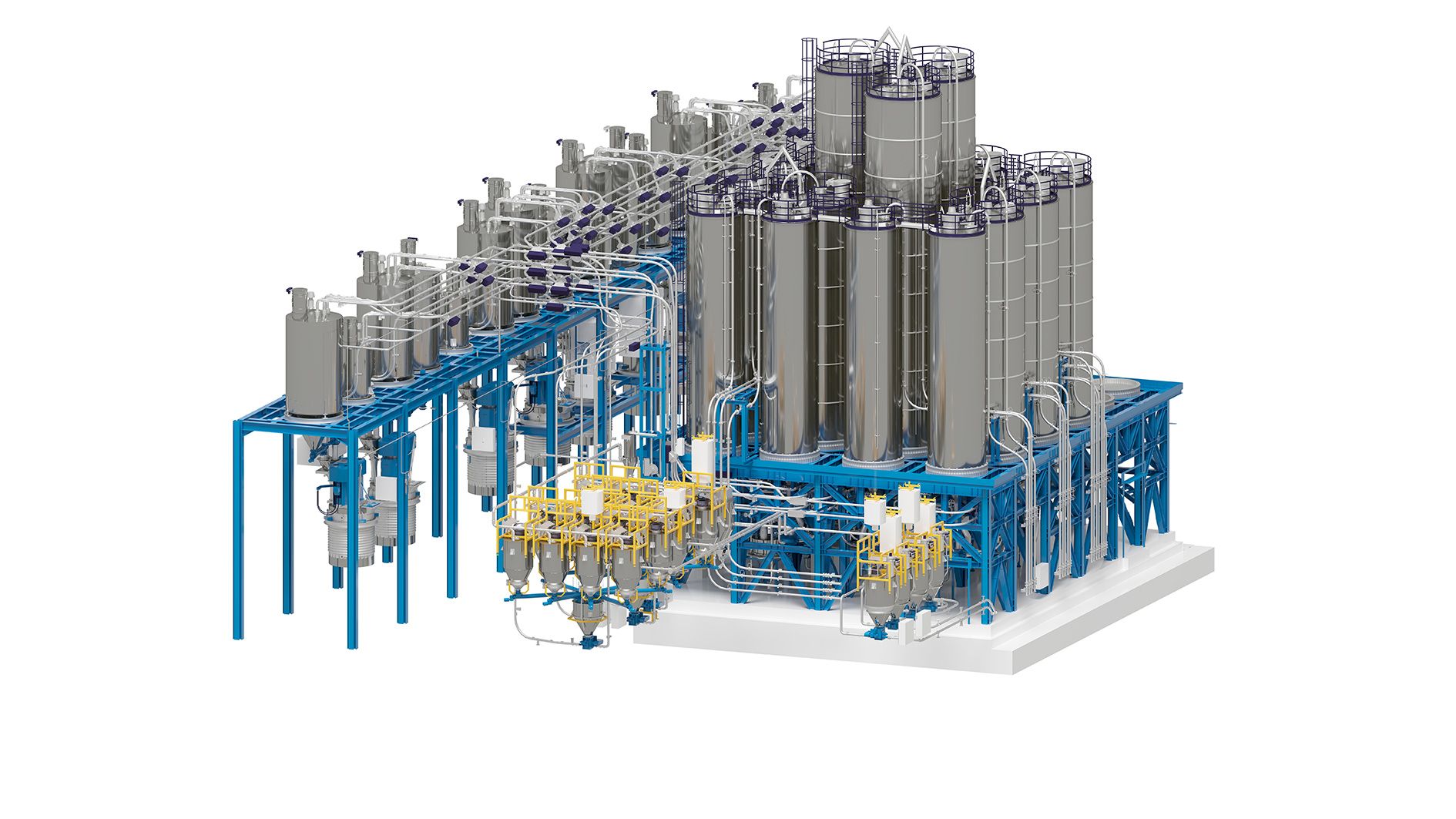
Zeppelin Systems präsentiert sich auf der European Coatings Show 2025
Zeppelin Systems zeigt auf der führenden Leitmesse für die internationale Lack- und Farbenindustrie, der European Coatings Show (ECS), seine Branchenexpertise. Im Mittelpunkt des Messeauftritts steht diesmal ein Prozessmischer für das Bonding sowie a...
Weiterlesen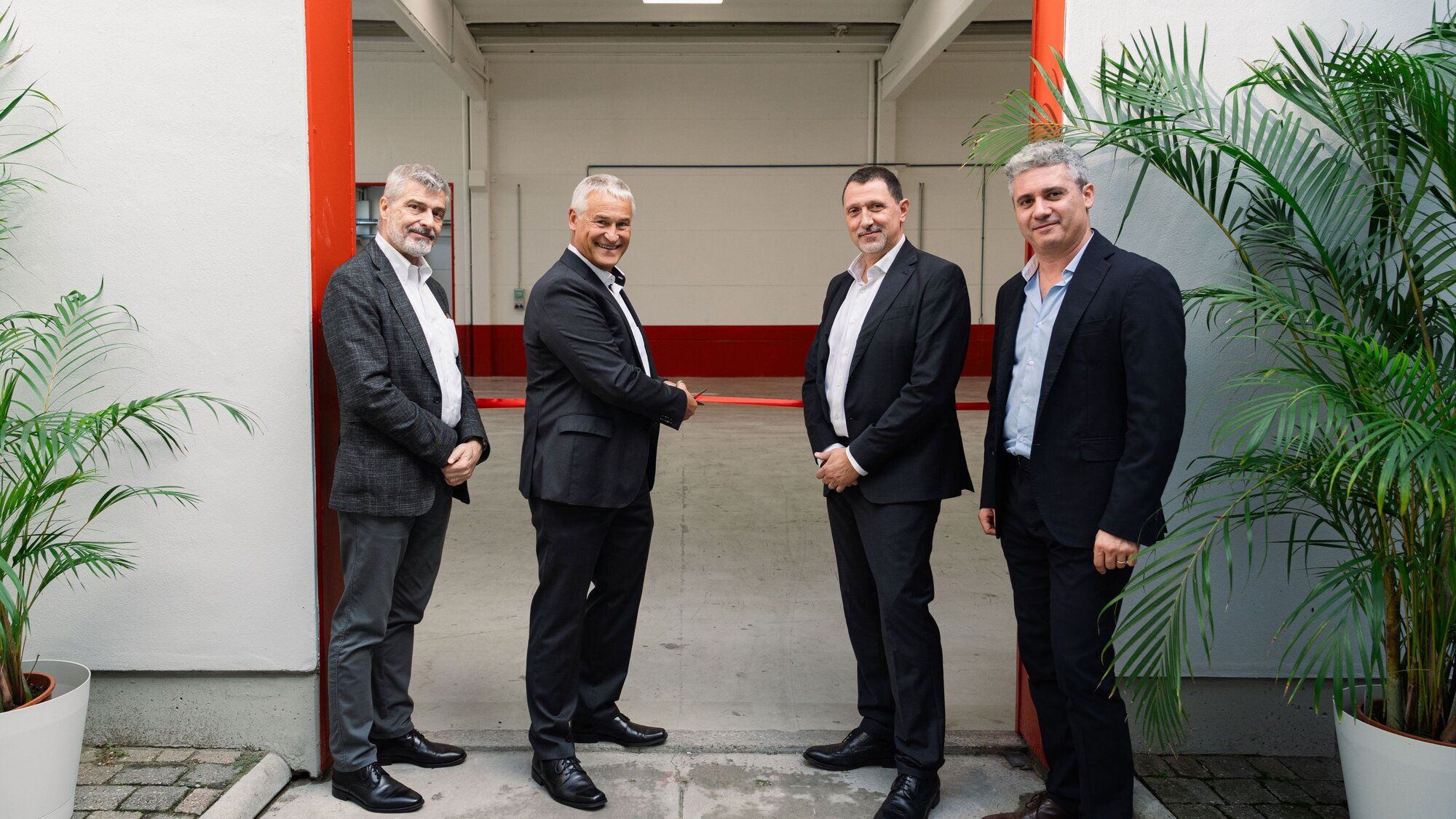
Zeppelin Systems verstärkt seine Präsenz in Italien
Gemeinsam mit dem im Jahr 2018 übernommenen Unternehmen Nuova Ciba ist Zeppelin Systems bereits seit vielen Jahren im italienischen Markt aktiv und bekräftigt sein Engagement nun mit der Einweihung und Eröffnung neuer, moderner Räumlichkeiten am Komp...
Weiterlesen
Zeppelin Systems präsentiert innovative Lösungen für die Batteriemassenproduktion beim Batteries Event in Lyon
Als führender Experte für die effiziente Aufbereitung von Rohstoffen stellt Anlagenbauer Zeppelin Systems in der französischen Stadt Lyon vom 16. bis 18 Oktober im Convention Centre an Stand C43 wegweisende Hochleistungs-Mischer, innovative Mischverf...
Weiterlesen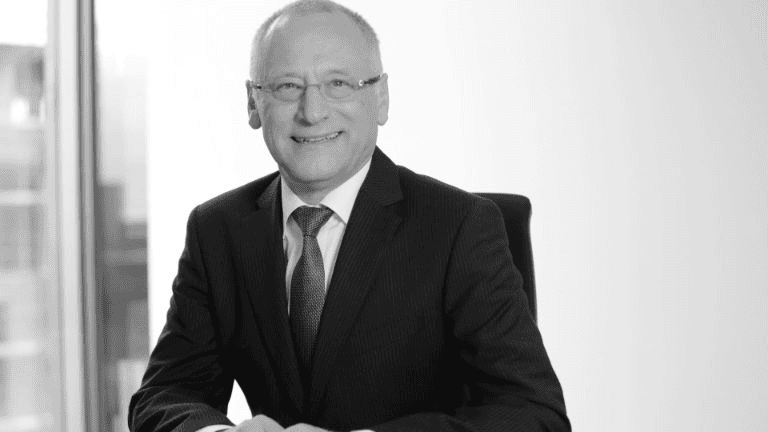
Zeppelin Systems trauert um ehemaligen Geschäftsführer Rochus Hofmann
Anlagenbauer Zeppelin Systems verabschiedete Rochus Hofmann nach knapp 20 Jahren an der Unternehmensspitze erst im Juli 2023 in den wohlverdienten Ruhestand. Am 8. September 2024 verstarb der allseits beliebte und geschätzte Geschäftsführer im Alter ...
Weiterlesen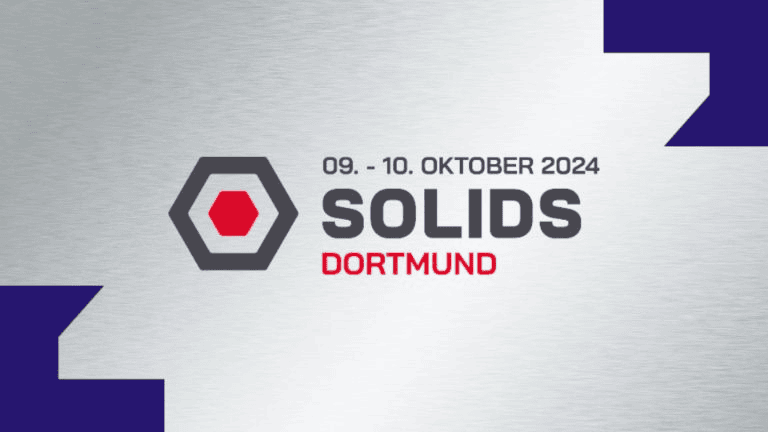
Zeppelin Systems hackt auf der Fachmesse Solids 2024 etwas aus
Die Fachmesse für Granulat-, Pulver- und Schüttguttechnologien in Dortmund hat sich in diesem Jahr etwas Besonderes einfallen lassen, um das internationale Publikum zu begeistern: Am 8. Oktober 2024 startet der Hackathon „Bulk Masters“ – das neue Mit...
WeiterlesenPressekontakt
Zeppelin Systems Unternehmen
Erfahren sie mehr über Zeppelin Systems
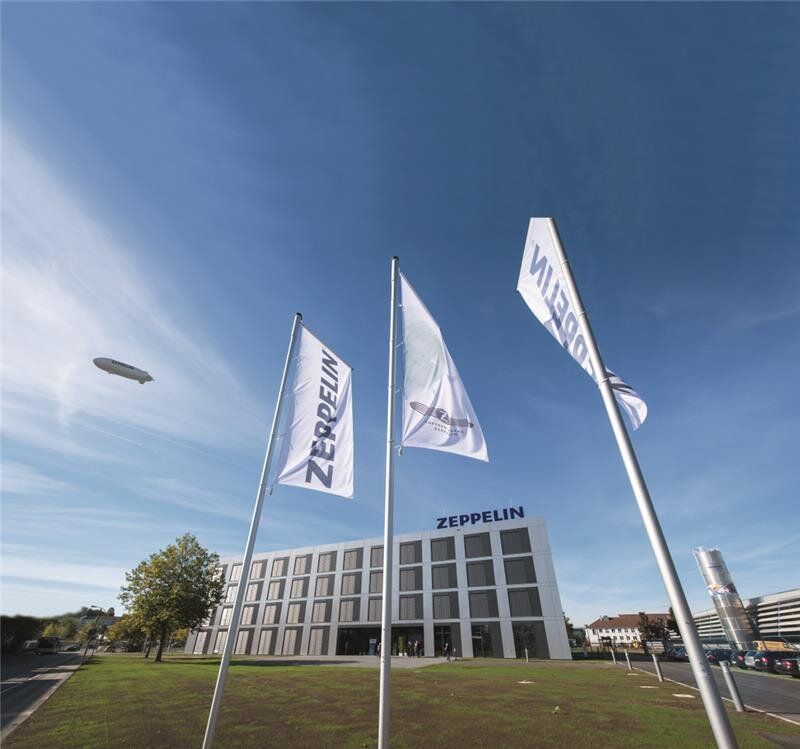
Über Zeppelin Systems
Erfahren Sie mehr über Anlagenbauer und Lösungsanbieter Zeppelin Systems!
Wer wir sind
Zahlen & Fakten über Anlagenbauer Zeppelin Systems
Die wichtigsten Informationen über Zeppelin Systems auf einen Blick.
Zu den Zahlen & FaktenUnternehmensgeschichte
Erfahren Sie mehr über die Vergangenheit von Zeppelin Systems.
Zur Unternehmensgeschichte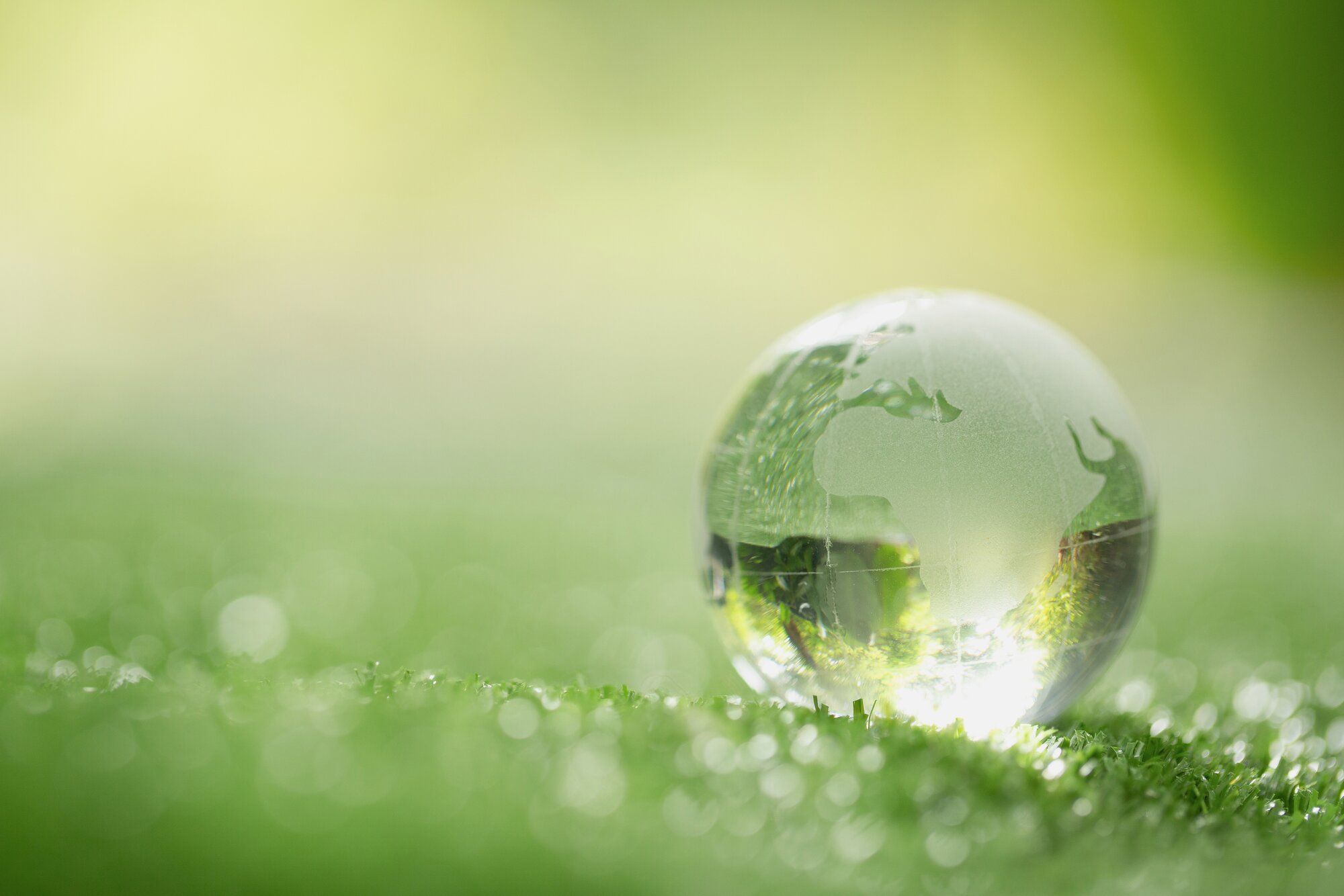
Nachhaltigkeit bei Zeppelin Systems
Unsere Verantwortung als Stiftungsunternehmen.
Zu unseren Nachhaltigkeits Maßnahmen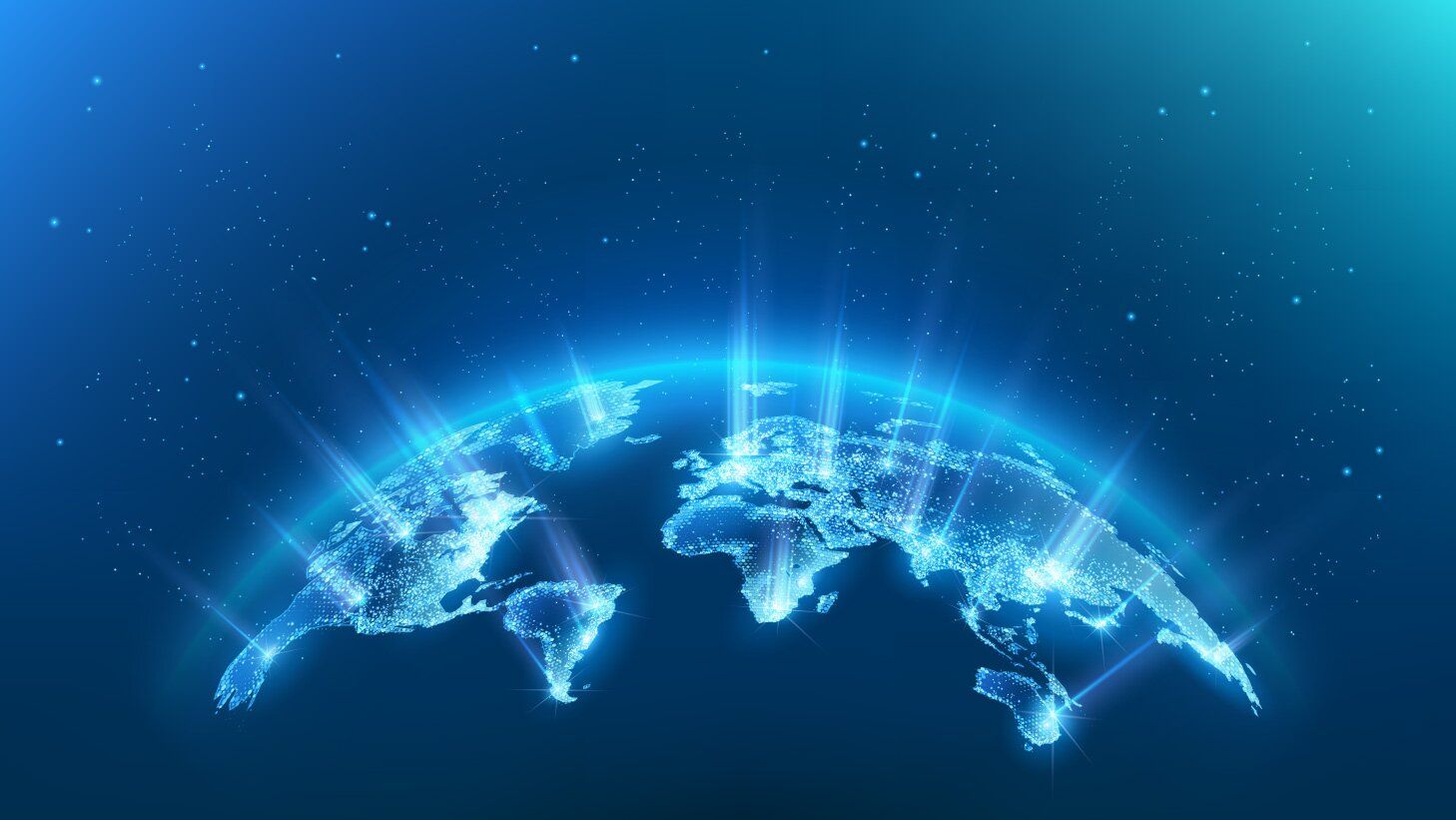
Zeppelin Systems weltweit – Standorte & Kontakt
Erfahren Sie mehr über Anlagenbauer und Lösungsanbieter Zeppelin Systems!
Zu unseren Standorten & Kontakt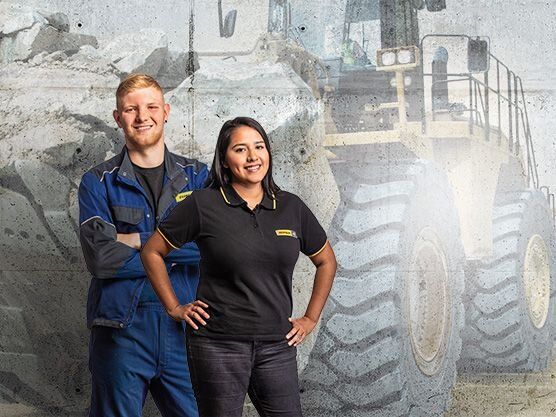
Karriere bei Zeppelin Systems
Wir sind immer auf der Suche nach Talenten! Besuchen Sie unter Stellenportal.
Zum Karriereportal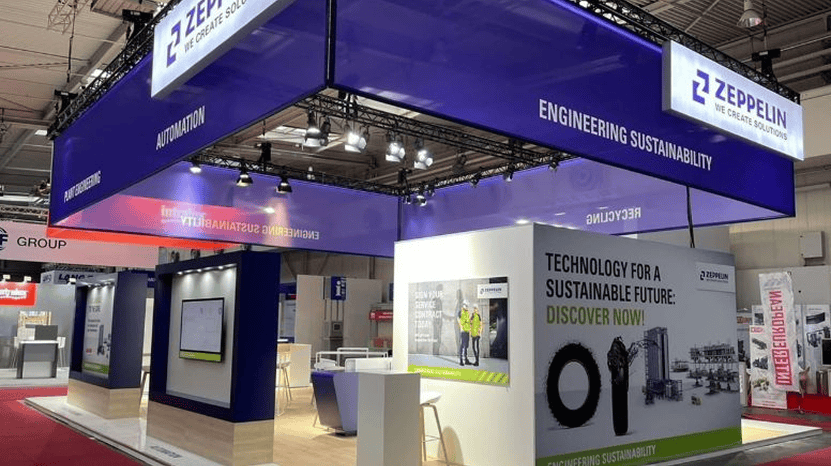
Messen & Events
Zeppelin Systems ist in seinen Branchen auf allen wichtigen Fachmessen weltweit vertreten – wir freuen uns, Sie auf der nächsten Messe begrüßen zu dürfen.
Zu den Messen & Events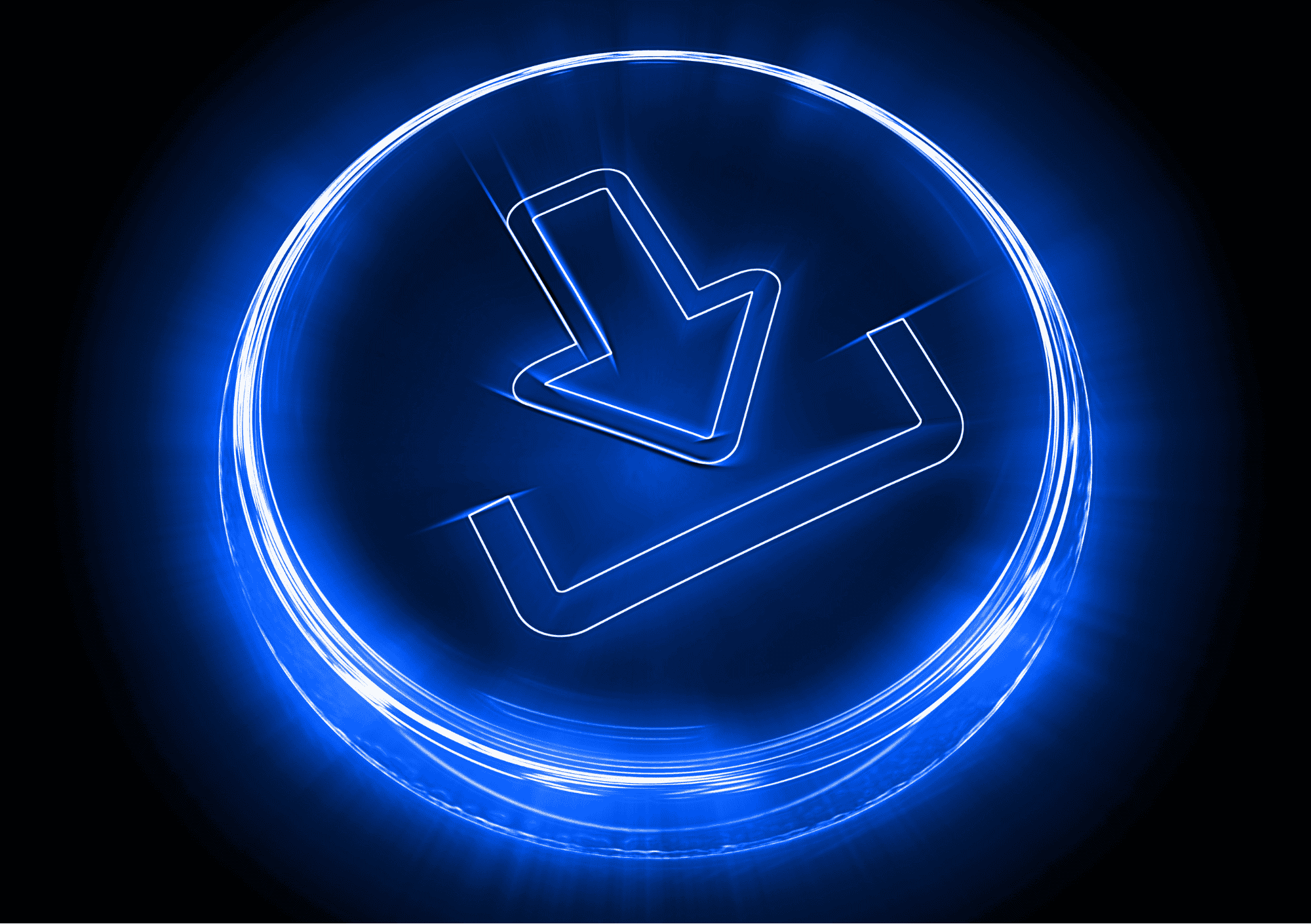
Downloads
Hier finden Sie eine Vielzahl von Broschüren und Datenblättern, um mehr über unsere Produkte und Dienstleistungen zu erfahren.
Zu den DownloadsInformieren
Unternehmen
Zeppelin Konzern
© 2025 Zeppelin Systems GmbH