Zeppelin Systems sets the pace for battery-mass production at the Battery Show 2024
29. May 2024 | Friedrichshafen
Zeppelin Systems is a global plant engineering company and a leading expert in the efficient processing of raw materials. It will be presenting powerful high-performance mixers, innovative mixing processes and efficient material handling and dosing systems for the production of battery masses at Europe’s largest trade fair for the battery industry, which will be held in Stuttgart from June 18 to 20. See for yourself the cumulative solutions competence and tailored customer solutions for efficient and safe raw material handling from Zeppelin Systems at stand 8-A75 at the Battery Show 2024. We Create Solutions!
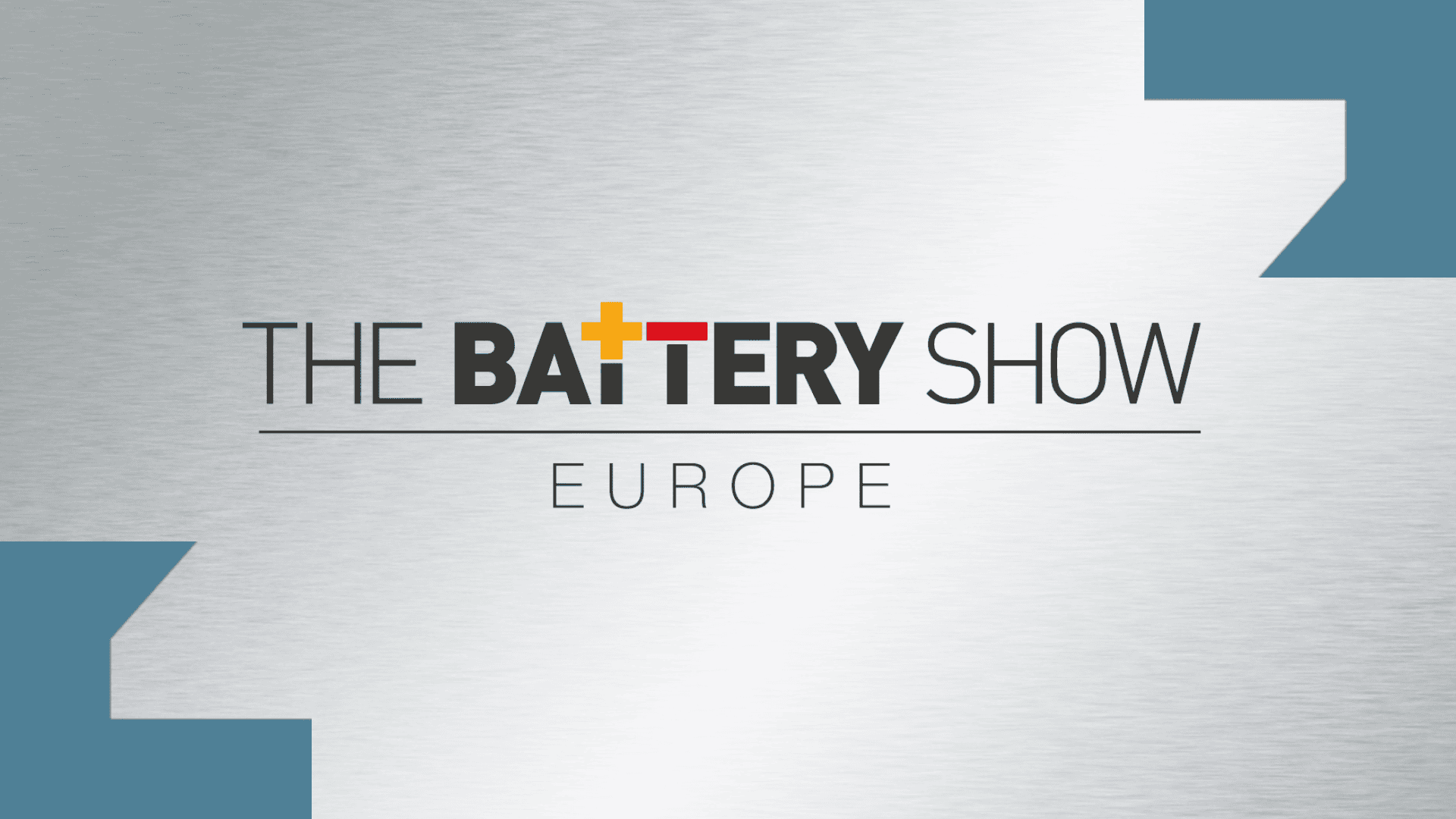
High Intensity mixers for optimal results
The powerful high-intensity mixers from Zeppelin Systems enable highly efficient dispersion and homogenization of raw materials. This makes them ideal for resource-conserving and safe production of battery masses in dry and semi-dry mixing process. In a variety of process steps with individual shear rates and temperature profiles, they can effectively disperse and finely distribute partly nanoparticulate conductive additives, and fibrillate and activate binder materials in a targeted way. In addition, a selective modification of the particle structure can increase the bulk density and energy density. Furthermore, the mixers offer customized wear protection, which ensures a long service life even with abrasive raw materials. “We have already impressed international battery customers with our high intensity mixers, and we are confident that we will be able to further expand this important future market,” says Dr. Markus Vöge, CEO of Zeppelin Systems GmbH, adding: “Thanks to our many years of industry experience, we are able to react quickly and flexibly to our customers’ requirements in battery-mass production,” adds the Head of Plant Engineering.
Advanced expertise in raw material handling
Raw material handling plays a major role in the production of dry-coated electrodes. Plant engineering company Zeppelin Systems also has a high level of expertise in this area. In addition to rapid emptying of a very wide range of containers, this also includes gentle pneumatic conveying without segregating the finished product. In addition, toxic raw materials are handled safely using sophisticated containment technology. The individual components are dosed into the mixer very 2 precisely and discharged reliably – thanks to the right discharge aid, even for raw materials that are difficult to fluidize. The Zeppelin Batch Management System ensures seamless batch traceability.
Calender dosing innovation
To ensure continuous and precise dosing of the calender rollers, Zeppelin Systems engineers developed their own calender dosing system. “The dosing unit for the calender has a continuous material supply with level monitoring in the hopper, which means that the calender rollers cannot run empty. The special geometry of the hopper prevents any bridging effect, and the development of dust from the hopper and vibration channel is also not an issue”, explains Hubert Stojanovic, Vice President for Performance Materials at Zeppelin Systems GmbH.
Testing and optimizing processes – in Zeppelin Systems’ technical department
Zeppelin Systems operates three test centers where process-critical processing steps can be tested and improved. One example is the Test Center for Mixing Technology in Kassel, where processes are developed and tested on individually configurable mixers at laboratory and production scale. For various AAMs (anode active materials) and CAMs (cathode active materials), such as LFP, NCA, NCM or graphite, test series have been carried out recently with various customers and research institutions. The various products’ behavior with regard to fluidizability, caking, discharge behavior, product destruction, etc. are investigated at the test center in Friedrichshafen. A separate test setup is currently being created here to enable calender dosing testing for various AAMs and CAMs for Zeppelin Systems customers. In addition, a very wide range of product analyses are carried out in the company’s own bulk material laboratory; these include moisture measurement, particle size and distribution, bulk density determination, and shear tests.
Projects with more than 150 gigawatts implemented to date
Zeppelin Systems’ battery-mass expertise is valued worldwide. Customer projects of over 150 GWh have been implemented to date in Germany, Sweden, the USA, India and South Korea. In addition, Zeppelin Systems is playing a key role in national and international research and development projects. Notable examples are the EU-funded GIGABAT project and the German GUTBatt project. GUTBatt involves process development of scalable material structuring as well as dry mixing and calendered dry electrode production for lithium-ion batteries with liquid and solid electrolytes. We Create Solutions!
Press contact
© 2025 Zeppelin Systems GmbH